Archive for the ‘Blog’ Category
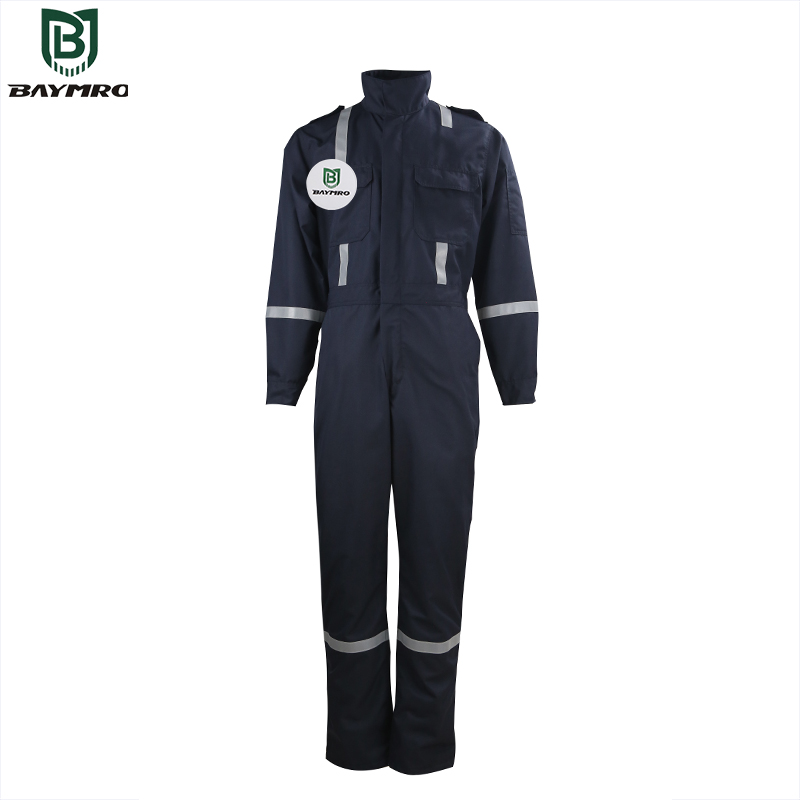
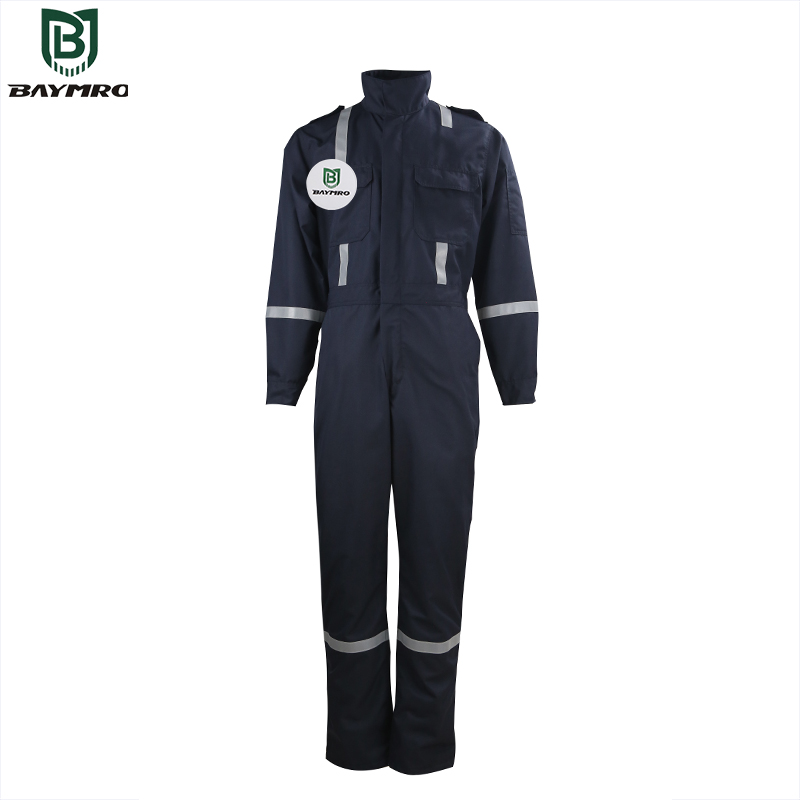
For safety managers in the oil & gas industry, flame resistant (FR) personal protective equipment (PPE) is an indispensable tool to help mitigate daily flash fire hazards. Given the variety of FR PPE options, it can be hard to understand the needs of your specific job site while sorting through the vast amount of information surrounding flash fire protection. It can be easy to remain with the status quo and not explore new and emerging options to bolster your FR apparel program.
An FR base layer is one such garment. When incorporated into an FR apparel system, it can provide benefits beyond what the name might suggest. As we disprove four myths surrounding this specific type of garment, we encourage you to analyze how FR base layers might enhance your FR system and even help foster a culture of responsible PPE use.
Myth 1: It does not matter what you wear underneath FR garments.
Simply stated, it matters a great deal what you wear underneath your FR garments. For those in the oil & gas industry, NFPA 2113, the companion standard to the consensus standard NFPA 2112, requires undergarments or base layers be made of flame resistant or non-melting fabric. So, while it is sufficient to wear non-melting fabrics like cotton, silk or wool, it is important to stay away from undergarments and base layers made with fabrics like acetate, nylon, polypropylene or spandex. These popular fabrics will melt when exposed to high temperatures consistent with a flash fire and can directly impact the insulation properties of FR garments. When these fabrics melt, heat is transferred to the skin, which can cause severe and even life-threatening burns.
Safety managers have the opportunity to increase the overall protection level of an FR garment system by adding an FR base layer. FR base layers help meet the requirements of NFPA 2113 with an approved, non-melting fabric that also helps mitigate repercussions of a flash fire incident. In addition, an FR base layer creates additional air gaps between layers of FR garments, increasing thermal insulation and heightening a system’s ability to provideinsulation from second- or third-degree body burns.
Myth 2: If you wear FR base layers, you can wear any type of outer layer garment.
The hallmark of FR fabrics is that they will self-extinguish when a thermal source, like a flash fire, is removed. For FR fabrics to play their part in overall flash fire protection, it is important that flammable fabrics in no way ignite should an incident occur. Flammable fabrics, as the name suggest, will continue to burn even after a flame is removed—compromising the self-extinguishing properties of FR garments.
Regardless of if you are wearing an FR base layer, you must ensure the outermost layer of the garment system is FR to comply with NFPA 2113. This outermost layer must cover any compliant but non-FR fabrics, so they will not ignite and continue to burn after a flash fire is over.
Myth 3: Another layer makes FR PPE less comfortable.
Enabled by advances in FR fabric technology, FR base layers now incorporate performance and comfort benefits once unthinkable in FR workwear. Some FR base layers can offer comfort-related benefits, like moisture-wicking and breathability properties. These base layers can provide additional warmth in the wintertime, helping to draw moisture away from the skin so a chill does not set in when a worker takes a break from a strenuous task. In the summer months, the same principle is applied to help wick sweat from the skin, allowing the body to better regulate its temperature.
FR base layers can enhance the overall wearability of an FR garment system, ideally balancing necessary protection and comfort characteristics to help foster a want-to-wear experience. If the clothing system is comfortable and does not detract from their ability to perform their jobs, workers are far more likely to be wearing all of their PPE gear for consistent on-the-job protection.
Myth 4: Daily wear garments, like FR base layers, cause workers to be more complacent about using their other task-based PPE.
Using daily wear FR PPE day in and day out can actually encourage workers to be more engaged with PPE use in general. Knowing that your workers carry a measure of consistent FR protection can complement worker engagement with the safety process. While FR daily wear is worn throughout the workday, other PPE like gloves and headgear, is worn only when the task demands and must be donned through conscious thought. Since FR daily wear, like shirts and pants, is worn throughout the day, it stands to reason that it can act as a reminder to don other task-based PPE as needed.
About the Author
Scott Francis is the Technical Manager for Westex by Milliken. This article originally appeared in the September 2019 edition of ISHN magazine.


Changes in Safety Shoe Standards and Basic Requirements
The European Union has approved the EN ISO 20345:2022 standard for “Personal Protective Equipment – Safety Shoes,” scheduled for release on April 30, 2022. This new standard will replace the EN ISO 20345:2011, granting it legal status in September 2022 and becoming fully mandatory on April 1, 2023.
What Does EN ISO 20345:2022 Encompass?
EN ISO 20345:2022 outlines both the fundamental requirements and optional requirements for general-purpose safety shoes. It also provides requirements for improved and personalized versions of safety shoes. The standard’s primary objective is to protect the wearer’s feet and legs from hazards in the workplace.
Key Changes and Additions
Treatment of Non-Metallic Toe Caps and Puncture-Resistant Insoles: The new standard introduces high and low-temperature and acid-alkali sweat immersion treatments for non-metallic toe caps and puncture-resistant insoles, making testing more reflective of real-world usage scenarios.
Product Categories: While the old standard recognized six product categories (SB, S1, S2, S3, S4, S5), the new standard offers further subdivision, introducing S3L, S3S, S5L, S5S, S6, S7, S7L, and S7S categories. S3L, S3S, S5L, S5S, S7L, and S7S are classified based on non-metallic puncture pins’ specifications.
Electrical Performance: The updated standard includes additional requirements for ladder-pattern slip-resistant outsoles to meet the needs of specific scenarios involving ladder climbing. Moreover, with the growing demand for customization, the new standard incorporates requirements for personalized footwear.
Slip Resistance Testing: The previous method included three testing requirements (SRA, SRB, SRC). The presence of the “Ø” symbol on the sole indicated no slip resistance testing was needed. In the absence of any symbols, meeting the conditions A and B requirements was sufficient. For soles with the “SR” symbol, both conditions C and D requirements had to be met in addition to A and B.
Should You Invest in New Safety Shoes?
Safety shoes are a critical component of personal protective equipment. To ensure that your footwear consistently provides optimal protection, they should be in good condition. Typically, employer liability insurance associations recommend replacing safety shoes regularly, especially when they are damaged in a way that compromises their protective function. However, in some jobs, shoes may experience significant wear and tear, necessitating more frequent replacements as needed. Employers typically cover the cost of new work shoes. You can assess the condition of your safety shoes based on EN ISO 20345 and decide whether it’s time to purchase a new pair.
When assessing the condition of safety shoes, pay attention to the following:
- Clearly visible and deep cracks affecting half the thickness of the shoe’s upper but not affecting the protective features.
- Severe wear of the shoe’s upper material, particularly in areas like the toe cap or midsole designed for puncture resistance.
- Deformation or separation of shoe upper seams.
- Cracks on the outsole that are longer than 10 mm and deeper than 3 mm.
- Tread depth, with any single tread point being less than 1.5 mm.
- Damage to the lining or toe cap.
- Gaps between the shoe upper and outsole longer than 15 mm and deeper than 5 mm.
- Further damage, such as material melting and fusion of two or more tread faces, tread depth reduced to less than 1.5 mm, melting of the outer edges of the tread with the midsole visible, noticeable deformation and compression of the original insole (if present), significant deformation of the outsole due to heat, abnormal fastening (zippers, laces, eyelets, hook-and-loop fasteners).
Conclusion
The adoption of the EN ISO 20345:2022 standard signifies significant improvements and additions to safety shoe requirements. As a responsible wearer of safety shoes, it’s crucial to regularly inspect and replace them when necessary to ensure your safety and protection in the workplace. Your employer typically bears the cost of acquiring new safety footwear, so make use of EN ISO 20345 guidelines to make informed decisions about the condition of your safety shoes. Prioritize your safety by keeping your footwear in excellent working condition.
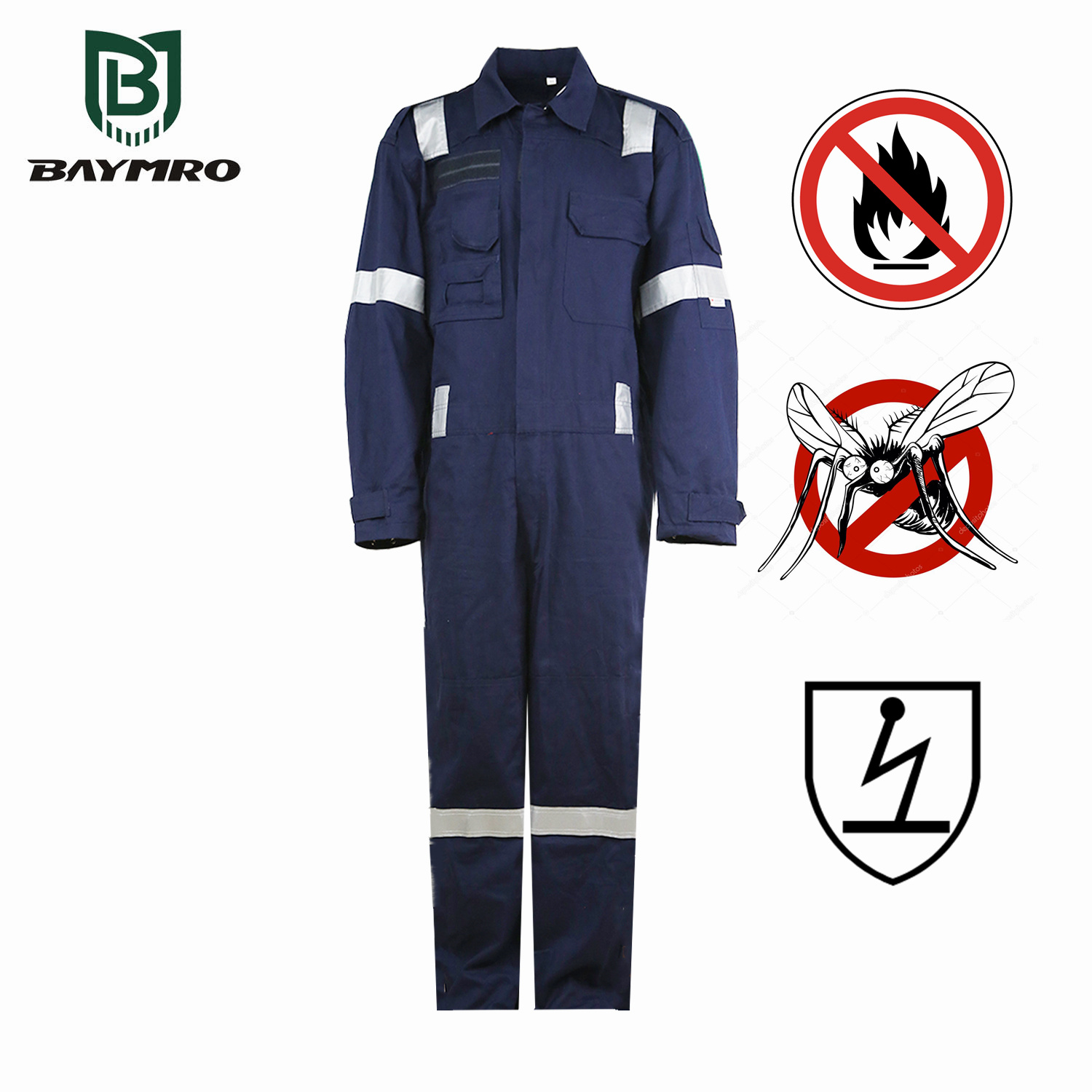
Introduction
In the realm of fashion, jumpsuits have always been recognized for their chic and stylish appearance. However, imagine a jumpsuit that not only elevates your fashion quotient but also incorporates cutting-edge technology to enhance functionality and safety. Enter the Anti-static anti-mosquito flame-retardant jumpsuit that boasts not one, not two, but three incredible functions: anti-static, flame retardant, and anti-mosquito properties. In this article, we delve into the captivating world of this innovative jumpsuit, exploring its diverse applications, the scenarios in which it shines, and the compelling reasons behind customers’ unwavering choice.
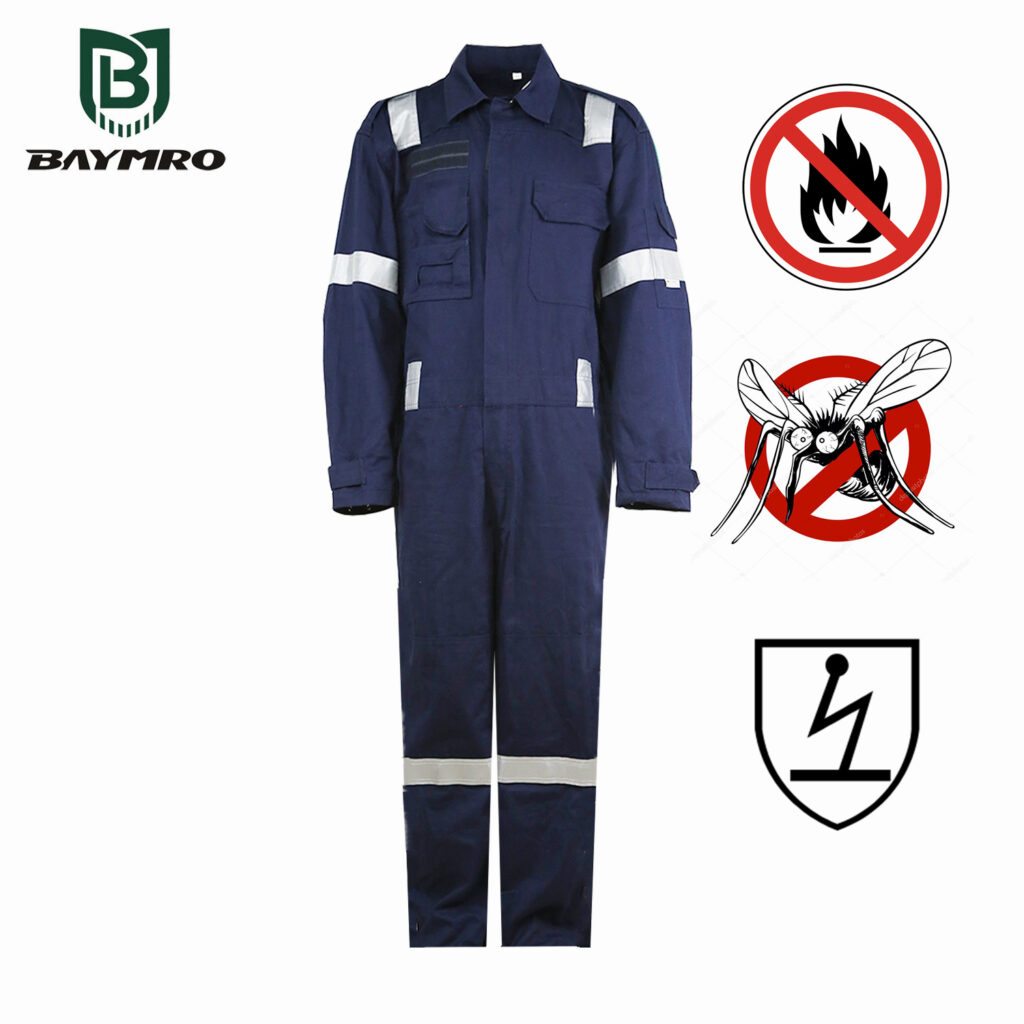
A Trio of Remarkable Features: Anti-Static, Flame Retardant, and Anti-Mosquito
At the heart of this jumpsuit’s appeal lies its unprecedented combination of three extraordinary features:
Anti-Static Magic: In work environments where static electricity can wreak havoc on sensitive equipment or cause discomfort, the anti-static function of this jumpsuit ensures that electric charges are safely dissipated. Bid farewell to accidental shocks and technical malfunctions!
Flame Retardant Guardian: Safety takes center stage in industries where flames and sparks are an ever-present concern. The flame retardant property of the jumpsuit acts as a guardian, significantly reducing the risk of burns and injuries in hazardous situations.
Anti-Mosquito Shield: Outdoor work or leisure activities often expose individuals to the annoyance of mosquito bites. With its anti-mosquito feature, this jumpsuit becomes a shield against these pesky insects, ensuring a comfortable and uninterrupted experience.
Versatile Utilization Scenarios
The allure of this Anti-static anti-mosquito flame-retardant jumpsuit is not limited to a specific industry or environment. Its remarkable capabilities open up a world of possibilities:
Industrial Fortitude: From manufacturing floors to construction sites, the jumpsuit’s anti-static and flame retardant properties offer a potent combination of protection and utility for workers.
Laboratories of Discovery: In research labs and testing facilities, the anti-static feature ensures precise experiments, while the flame retardant property safeguards against unforeseen chemical mishaps.
Outdoor Enthusiasts: Nature lovers, adventurers, and explorers can now revel in their escapades without the constant nuisance of mosquitoes. The anti-mosquito feature makes outdoor activities a joyous affair, free from the irritation of insect bites.
Technical Expertise: Professionals in fields like electronics repair, aerospace engineering, and even emergency response services can leverage the multifaceted nature of this jumpsuit to enhance their efficiency and safety.
Decoding Customer Preference
The meteoric rise in the popularity of this Anti-static anti-mosquito flame-retardant jumpsuit can be attributed to several compelling reasons:
Safety First: The promise of a jumpsuit that prioritizes safety through its anti-static and flame retardant functions resonates deeply with customers working in potentially dangerous environments.
Efficiency and Focus: Outdoor enthusiasts and adventurers value the anti-mosquito feature, which lets them concentrate on their pursuits without the distraction of buzzing insects.
Convenience Redefined: The versatility of this jumpsuit eliminates the need for separate workwear or protection, simplifying wardrobe decisions and enhancing convenience.
Long-Term Value: Customers appreciate the durability of this jumpsuit, which ensures that its anti-static, flame retardant, and anti-mosquito functions remain effective for an extended period, offering exceptional value for money.
Innovation meets Style: Beyond functionality, this jumpsuit seamlessly merges innovative technology with contemporary fashion, allowing customers to make a statement without compromising on safety.
Conclusion
In the era of ever-evolving fashion, the introduction of the three-in-one jumpsuit heralds a new dawn in workwear innovation. The convergence of style and functionality, manifested through anti-static, flame retardant, and anti-mosquito properties, has captivated the hearts of individuals across various industries and interests. Whether you’re navigating the complexities of an industrial setting, conducting experiments in a lab, or embarking on an outdoor escapade, this Anti-static anti-mosquito flame-retardant coverall is your ultimate companion. It’s more than just clothing; it’s a testament to human ingenuity, a symbol of safety, and a beacon of convenience that is poised to revolutionize the way we perceive workwear.
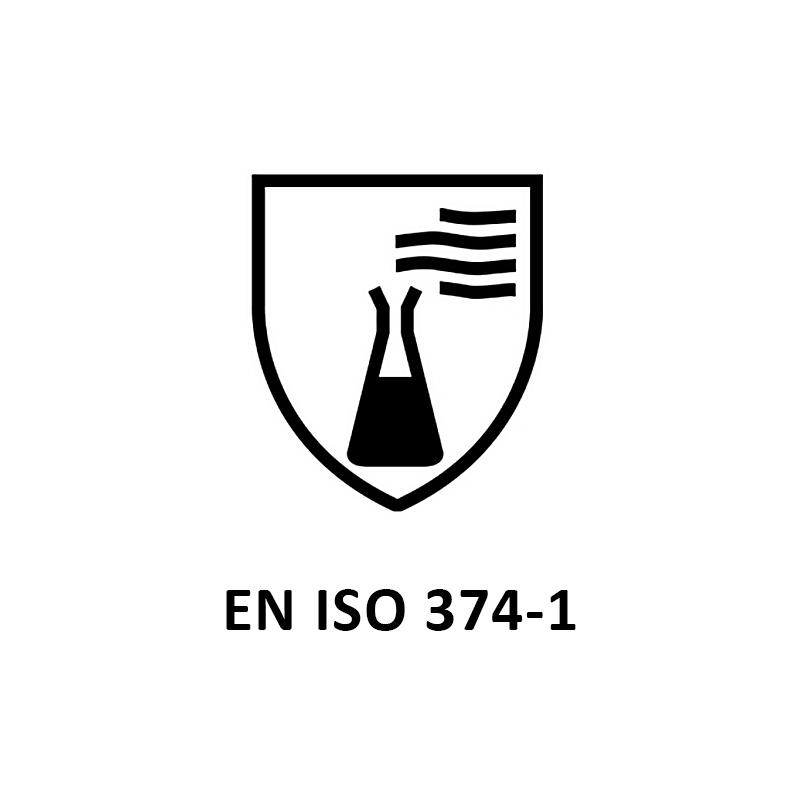
In a world where safety and protection are paramount, standards play a vital role in ensuring products meet stringent quality and performance standards. When it comes to protective gloves, one of the most frequently searched standards is EN ISO 374. This comprehensive guide aims to clarify key aspects of EN ISO 374, address common issues and clarify its importance in protecting hands from various hazards.
What is EN ISO 374?
EN ISO 374 is an important European standard that specifies the requirements for protective gloves designed to protect the wearer against hazardous chemicals and microorganisms. These gloves are widely used in industries where workers are exposed to hazardous substances such as chemicals, biological agents and viruses.
Why is EN ISO 374 important?
The importance of EN ISO 374 lies in its role in safeguarding the health and safety of workers. Exposure to hazardous chemicals and microorganisms can cause serious health problems ranging from skin irritations to life-threatening illnesses. Gloves complying with EN ISO 374 are rigorously tested to ensure they are effective against these risks.
What hazards does EN ISO 374 address?
EN ISO 374 mainly addresses two categories of hazards: chemical and microbiological. Chemical hazards cover a wide variety of substances, including acids, solvents, oils, and more. Microorganisms include bacteria, viruses and fungi, which are of particular concern in healthcare and laboratory settings.
How is EN ISO 374 testing performed?
Gloves are subjected to a battery of tests to assess their resistance to penetration, degradation and penetration. Penetration testing measures the time it takes for a chemical to penetrate the glove material, while degradation testing evaluates the physical changes to the glove after contact. Penetration testing evaluates a glove’s resistance to liquid and microbial intrusion.
What do the EN ISO 374 symbols mean?
EN ISO 374 Gloves are marked with a series of symbols indicating their performance against specific chemicals. These symbols consist of letters and numbers corresponding to the list of defined chemicals. Breakthrough times and penetration rates are indicated, providing the user with important information about the protective capabilities of the glove.
Are EN ISO 374 gloves reusable?
Whether a glove is reusable depends on its specific classification. Some EN ISO 374 gloves are designed for single use and must be disposed of after exposure to hazardous substances. Others are designed for multiple uses, and the manufacturer provides guidelines for proper decontamination and storage.
Is virus protection included in EN ISO 374?
Although EN ISO 374 was not originally designed with virus protection in mind, the standard’s test methods can be adapted to evaluate the barrier performance of gloves against viruses. However, it is worth noting that achieving virus protection requires specific testing for the relevant viruses, which may fall under different standards or certifications.
In summary:
EN ISO 374 is the cornerstone in the field of protective gloves, providing a standardized framework for evaluating the ability of gloves to protect against hazardous chemicals and microorganisms. The widespread interest in the standard is evidence of the growing awareness of workplace safety and the need for reliable protective equipment. By understanding the intricacies of EN ISO 374 and the information conveyed by its symbols, users can make informed decisions to ensure their safety and well-being in hazardous environments.
Introduce
In a world where safety is paramount, protective gear plays a vital role in protecting us from potential dangers. EN388 is a beacon of protection when it comes to choosing the right glove for tasks ranging from handling sharp objects to abrasive surfaces. In this article, we take a deep dive into EN388, demystify it, and provide insights so you can make an informed decision about protective gloves.
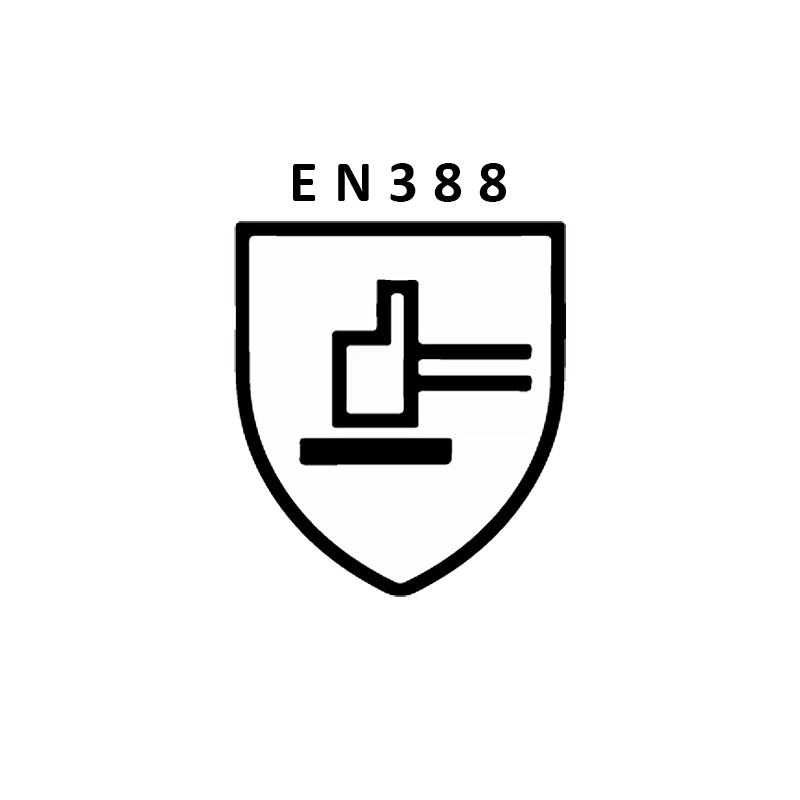
Uncovering EN388: Safety Language
Imagine if a glove could communicate its protective capabilities to you in a clear and concise manner. This is exactly what EN388 does. EN388 is more than just a standard; this code speaks volumes about the ability of gloves to protect hands from mechanical risks. By analyzing this code, you can unlock a wealth of information about the glove’s performance.
The Power of Numbers: Decoding EN388 Ratings
EN388 uses a numerical rating system to provide a comprehensive assessment of glove effectiveness in four key areas:
Abrasion Resistance (0-4): This number indicates how well the glove withstands abrasion. The higher the number, the greater the resistance.
Blade Cut Resistance (0-5): The second number evaluates the glove’s ability to resist sharp objects. Higher numbers indicate better cut resistance.
Tear Resistance (0-4): The number here emphasizes how durable the glove is against tearing forces. Higher numbers indicate increased tear resistance.
Puncture Resistance (0-4): This rating quantifies the glove’s ability to resist puncture by sharp objects. The higher the number, the better the puncture resistance.
EN388: Beyond numbers
EN388 doesn’t just stop with numbers; it extends its scope with symbols that provide supplementary information:
Impact Protection (P): The “P” symbol indicates that the glove provides additional impact protection, making it ideal for tasks involving striking objects.
Protection Against Rotating Machinery (T): When you spot the “T” symbol, it means the glove is designed to prevent cut hazards from rotating machinery.
Interpreting EN388 marking
Imagine a glove marked “4542”. Let’s break down what this code reveals:
Abrasion resistance: level 4 (strong protection)
Blade Cut Resistance: 5 (Excellent Cut Protection)
Tear strength: Grade 4 (strong tear strength)
Puncture Resistance: 2 (good puncture protection)
Protection against rotating machinery: T (cut hazard)
Impact Protection: P (additional impact protection)
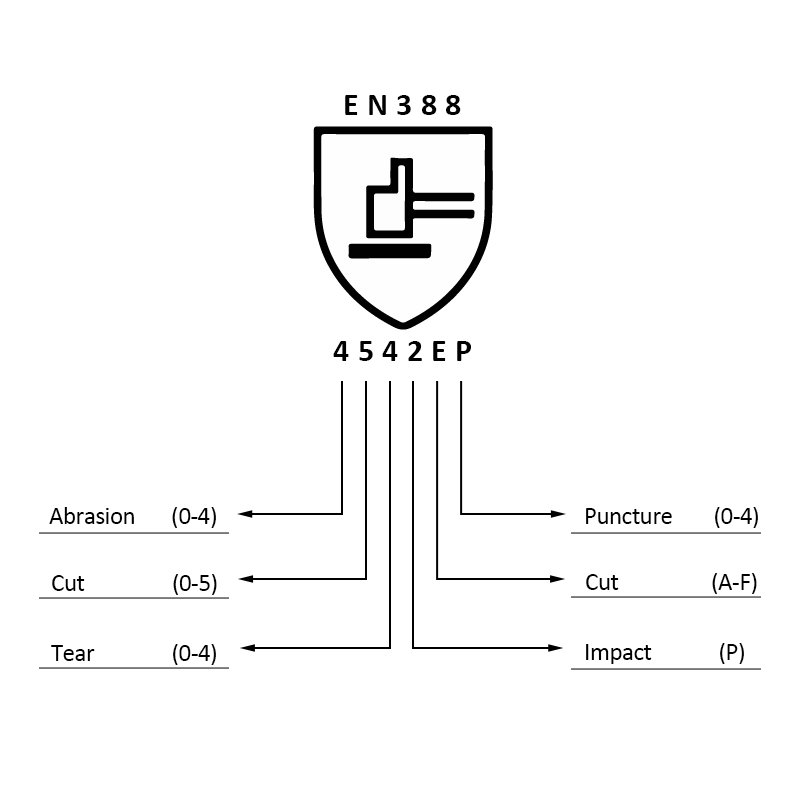
Why EN388 is your safety ally
EN388 translates complex technical details into a user-friendly format. It provides you with the knowledge to choose gloves that match the risks you face in your specific work environment. Whether you’re dealing with sharp blades, abrasive surfaces or machinery, EN388 guides your hands to optimal protection.
Conclusion: Improve Your Security Level
EN388 is more than a code; it’s your gateway to informed decisions. EN388, with its numerical rating and symbols, ensures you are not only wearing gloves, but wearing the correct gloves. Whether you’re a professional in a hazardous industry or a DIY enthusiast tackling household projects, EN388 can help you make an informed choice of gloves that provide custom protection.
From understanding its number system to embracing its symbols, EN388 enables you to elevate your safety levels. Don’t just wear gloves; embrace the language of safety with EN388 as your guide.
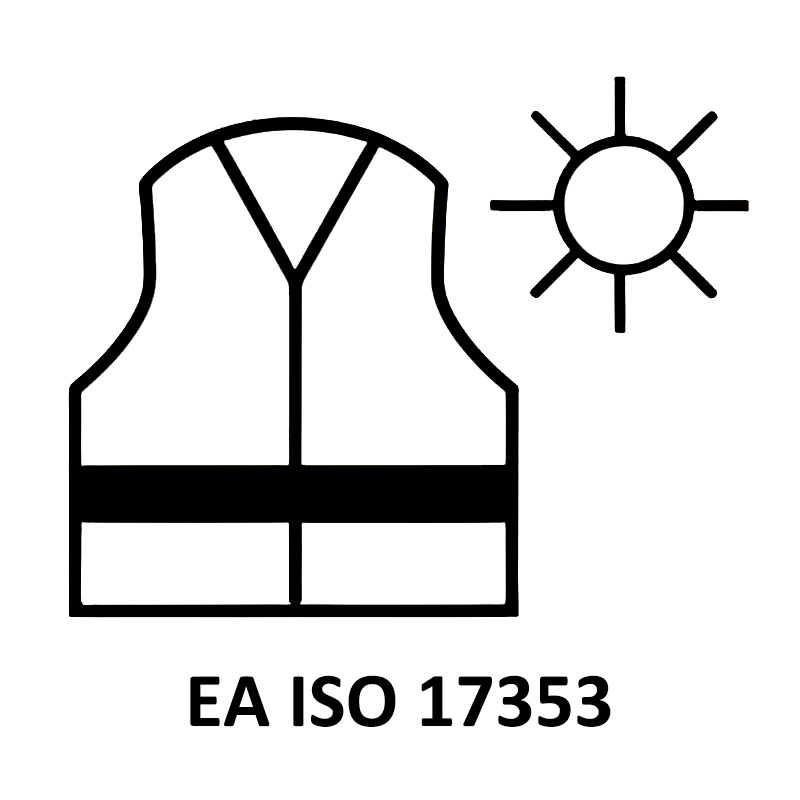
EN 17353:2020 standard supersedes two separate standards: EN 1150:1999 – ‘Protective clothing. Visibility clothing for non-professional use. Test methods and requirements’ – and EN 13356:2001 – ‘Visibility accessories for non-professional use. Test methods and requirements, both of which have now been withdrawn from use.
EN 17353 brings together elements of each of the withdrawn standards. However, all products meeting the requirements of the standard are no longer considered in terms of their use. Instead, their suitability in providing protection in medium risk situations is defined by their enhanced visibility properties.
The EN 17353 standard has also been devised to allow manufacturers more freedom in the design of products, given that enhanced visibility garments and devices are not intended for high-risk situations. Additionally, garments and devices are permitted for use in daylight (day) conditions only, dark (night) conditions only, or for both daylight and dark conditions.
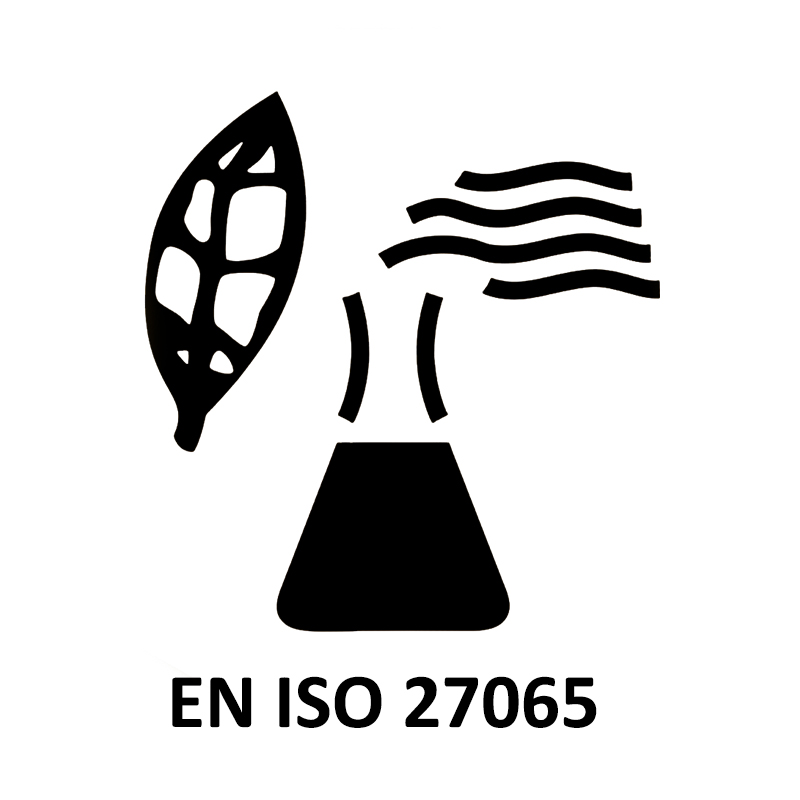
Protective clothing — Performance requirements for protective clothing worn by operators applying pesticides and for re-entry workers
ISO 27065 establishes minimum performance, classification, and marking requirements for protective clothing worn by operators handling pesticide products as well as re-entry workers. For the purpose of ISO 27065, the term pesticide applies to insecticides, herbicides, fungicides, and other substances applied in liquid form that are intended to prevent, destroy, repel, or reduce any pest or weeds in agricultural settings, green spaces, roadsides, etc. It does not include biocidal products used for agricultural and non-agricultural settings.
Pesticide handling includes mixing and loading, application, and other activities such as cleaning contaminated equipment and containers. Concentrated pesticides are typically handled during mixing and loading. Protective clothing covered by ISO 27065includes, but is not limited to, shirts, jackets, trousers, coveralls, aprons, protective sleeves, caps/hats and other headwear (excluding hard hats made of rigid materials, e.g. hats worn by construction workers), and accessories used under knapsack/backpack sprayers.
ISO 27065 does not address items used for the protection of the respiratory tract, hands, and feet. ISO 27065 does not address protection against fumigants.
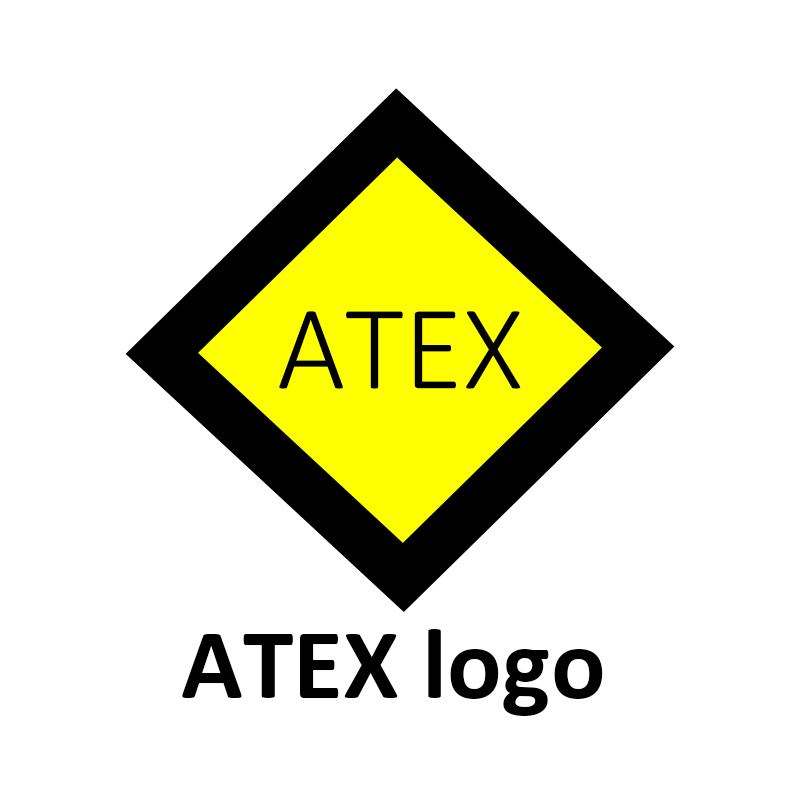
The ATEX logo is a recognizable symbol used to indicate products that comply with the European Union’s directives regarding equipment and protective systems intended for use in potentially explosive atmospheres. ATEX stands for “ATmosphères EXplosibles,” and the directives are designed to ensure the safety of equipment and systems used in environments where there is a risk of explosion due to the presence of flammable gases, vapors, mists, or combustible dusts.
The ATEX logo consists of an uppercase “Ex” within an oval or circular shape. The “Ex” stands for “explosion protection.” The logo is often accompanied by additional markings and information to indicate the specific compliance level, category, and sometimes the name of the notified body that certified the product.
The ATEX directives include two main categories:
- ATEX Directive 2014/34/EU (Equipment Directive): This directive covers equipment, devices, and protective systems intended for use in potentially explosive atmospheres. It defines requirements for manufacturers to ensure their products are safe and suitable for such environments.
- ATEX Directive 1999/92/EC (Worker Protection Directive): This directive focuses on the safety of workers who are operating in potentially explosive atmospheres. It outlines measures to protect workers from the risks associated with explosive atmospheres.
Products that comply with the ATEX directives are marked with the ATEX logo to signify that they have undergone the necessary conformity assessment procedures and meet the relevant safety requirements for use in explosive atmospheres. These products are commonly used in industries such as chemical, petrochemical, mining, pharmaceuticals, and more, where the risk of explosions must be managed carefully.

EN 15797 is a European standard that pertains to industrial washing of workwear and other textile products used in a professional context. The title of the standard is “Textiles – Industrial washing and finishing procedures for testing of workwear.” It falls under the category of textiles and is intended to provide guidelines and procedures for testing the industrial washing and finishing of workwear and other textile items.
EN 15797 specifies the requirements and testing methods for assessing the performance of workwear and similar textile products when subjected to industrial washing and finishing processes. The standard aims to ensure that workwear maintains its quality, performance, and appearance after being laundered using industrial methods.
The main parameters covered by EN 15797 include:
- Mechanical Action: The standard outlines procedures for testing the mechanical action of washing and drying on the textiles, which can impact their durability and appearance.
- Chemical Action: EN 15797 addresses the effects of detergents, chemicals, and water hardness on the textiles during the washing process.
- Thermal Action: The standard considers the effects of high temperatures during the drying process and how they may affect the textile items.
- Dimensional Change: EN 15797 includes tests to assess whether the textiles experience significant dimensional changes (shrinkage, stretching, etc.) after industrial washing and finishing.
- Color Fastness: The standard evaluates the textiles’ colorfastness to ensure that colors do not fade or bleed excessively during the washing process.
EN 15797 provides information and procedures for both pre-washing and post-washing assessments of textiles, and it is particularly relevant for industries that require durable and reliable workwear, such as those involving manual labor, industrial processes, and other professions.
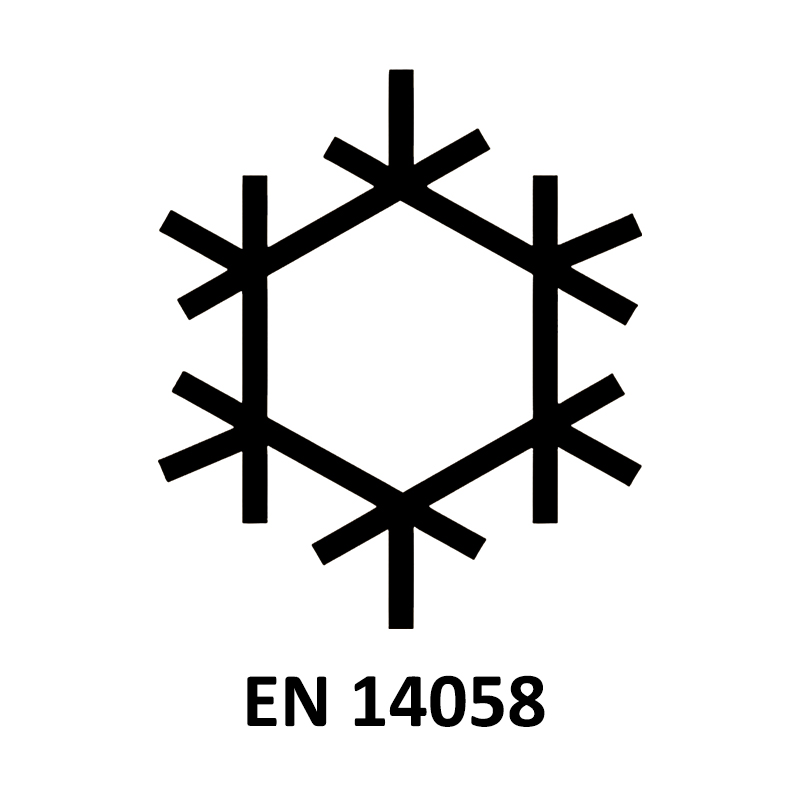
EN 14058 is a European standard that pertains to protective clothing designed to provide protection against cold environments, including both air temperature and wind conditions. The title of the standard is “Protective clothing – Garments for protection against cool environments.” It falls under the category of personal protective equipment (PPE) and is intended to ensure that protective clothing worn in cold conditions offers effective insulation and protection to the wearer.
EN 14058 specifies the requirements and testing methods for protective clothing garments that are designed to protect against cool environments, including both cold air temperatures and wind chill effects. The standard aims to ensure that workers exposed to cool conditions are adequately protected from the hazards of cold stress, which can lead to discomfort, reduced body temperature, and other health issues.
The main parameters covered by EN 14058 include:
- Thermal Insulation: The clothing’s ability to provide thermal insulation is tested to ensure it offers adequate protection against heat loss in cool conditions.
- Air Permeability: This parameter evaluates the clothing’s resistance to wind penetration, which is important to prevent wind chill and maintain warmth.
- Water Vapor Resistance: The standard assesses the clothing’s ability to allow water vapor (perspiration) to escape while preventing external moisture from entering. This is important to maintain comfort and prevent dampness.
- Resistance to Water Penetration: EN 14058 includes a test for resistance to water penetration to assess the garment’s ability to resist moisture.
- Optional Requirements: The standard also provides optional requirements for additional features such as breathability, moisture management, and visibility.
EN 14058 categorizes protective clothing into different performance levels based on its ability to provide thermal protection against cool conditions. The clothing is assigned a four-digit code that indicates its thermal insulation, air permeability, and water vapor resistance properties.
For example, the code “X3Y2Z1” could represent a garment that offers moderate thermal insulation (X3), low air permeability (Y2), and moderate water vapor resistance (Z1).