Archive for the ‘Blog’ Category
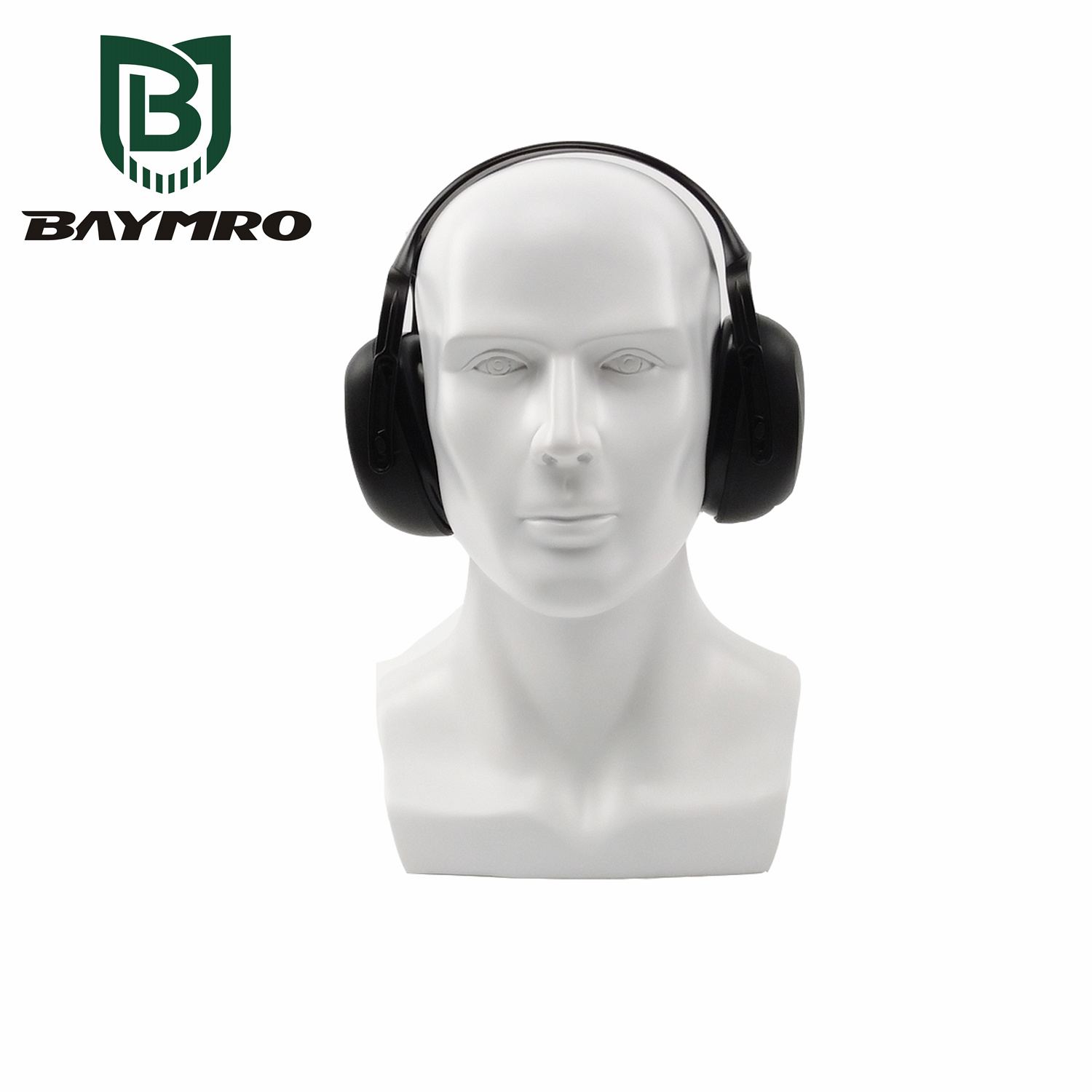
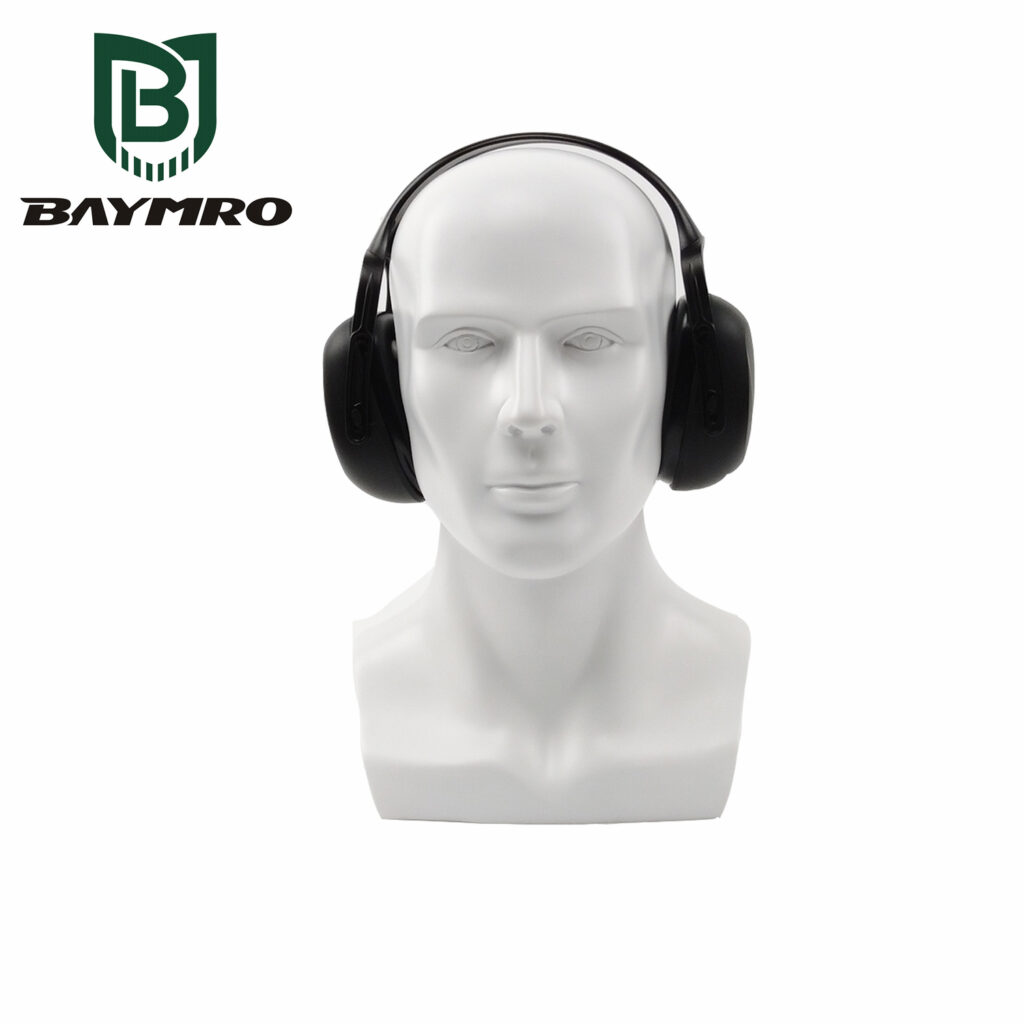
ANSI S3.19-1974 is an American National Standard for hearing protection devices (HPDs). Specifically, it provides guidelines and specifications for the measurement of the attenuation of earplugs and earmuffs used as hearing protection against occupational noise exposure.
Key points covered in ANSI S3.19-1974 include:
Attenuation Measurements: The standard outlines procedures and methods for measuring the attenuation or noise reduction capabilities of earplugs and earmuffs. Attenuation is the reduction in the intensity of sound that reaches the wearer’s ears when using these devices.
Test Subjects: ANSI S3.19-1974 specifies the criteria for selecting test subjects, including factors like age, gender, and prior experience with hearing protection devices. These criteria ensure that the testing represents a range of potential users.
Test Equipment: The standard describes the equipment and facilities needed for conducting attenuation measurements. This includes the use of acoustic test chambers or other controlled environments.
Testing Conditions: ANSI S3.19-1974 details the testing conditions and parameters, such as the specific noise levels used during testing and the procedures for fitting earplugs or earmuffs on test subjects.
Data Analysis: The standard provides guidance on how to collect and analyze the data obtained during attenuation measurements. This includes calculations for determining the Noise Reduction Rating (NRR) for earplugs and earmuffs.
Reporting: ANSI S3.19-1974 specifies the information that should be included in test reports, including details about the test subjects, equipment used, testing conditions, and the results of the attenuation measurements.
Quality Control: The standard emphasizes the importance of quality control measures to ensure accurate and repeatable attenuation measurements.
The Noise Reduction Rating (NRR), which is commonly found on the packaging of hearing protection devices, is typically determined using the methodology outlined in ANSI S3.19-1974. The NRR provides users with an estimate of the level of noise reduction they can expect when using a specific hearing protection device. Keep in mind that the NRR is a standardized value and may not represent real-world performance for all individuals, as actual attenuation can vary based on factors like fit and usage.
It’s important to note that standards and regulations can change or be updated over time, so it’s advisable to consult the most current versions of standards and guidelines for hearing protection devices if you need to ensure compliance with the latest industry requirements.
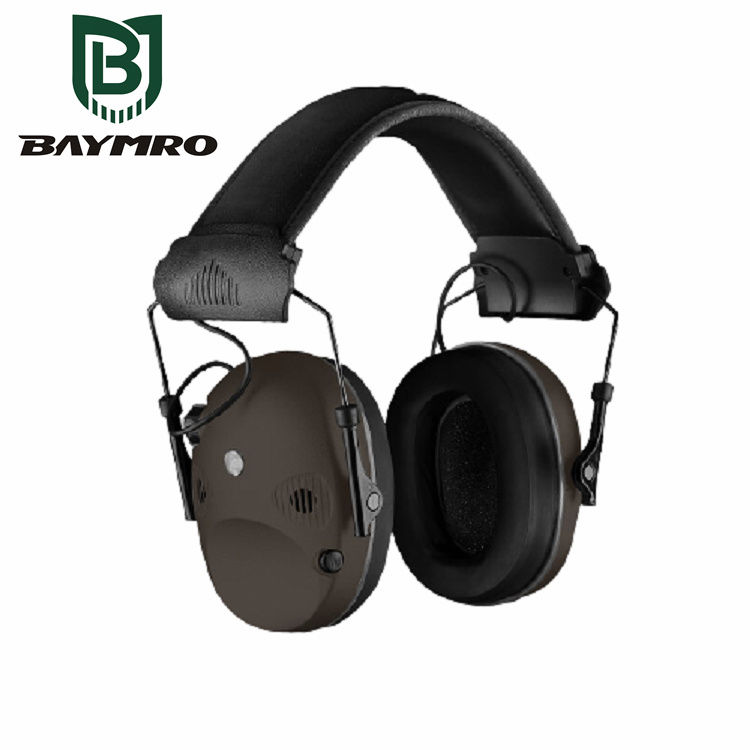
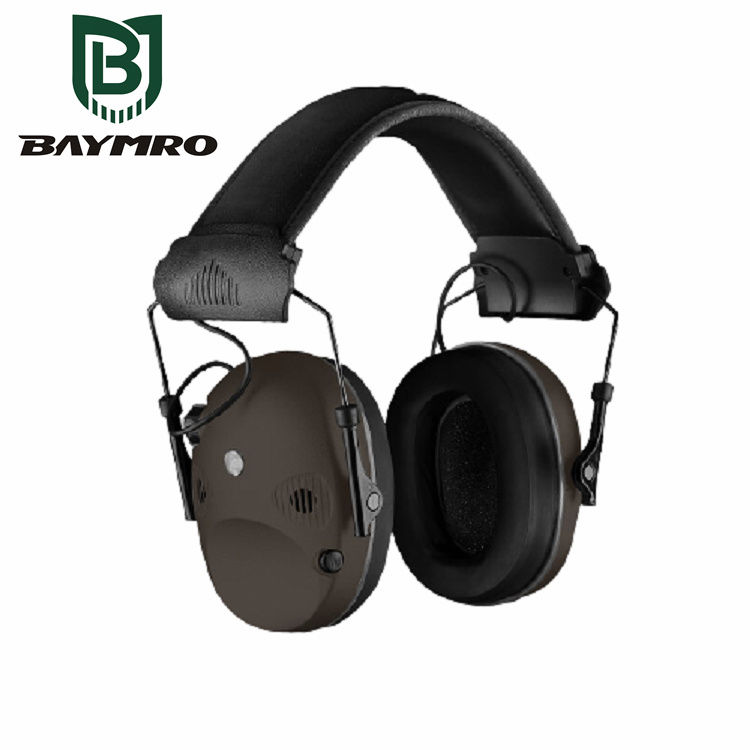
EN 352-4 is a European standard that specifies requirements and testing methods for level-dependent hearing protectors, often referred to as “Level-Dependent Earmuffs.” These hearing protectors are designed to offer variable protection, depending on the level of ambient noise, allowing wearers to hear low-level sounds while protecting against high-level noise. EN 352-4 ensures that these devices meet safety and performance standards. Here are the key aspects of EN 352-4:
Noise Reduction Rating (NRR): EN 352-4 specifies minimum requirements for the noise reduction performance of level-dependent earmuffs. The NRR indicates how effectively the earmuffs reduce the intensity of high-level noise, while still allowing lower-level sounds to be heard.
Frequency Range: The standard defines the frequency range over which the earmuffs must provide adequate protection. This range typically covers the frequencies where most occupational and environmental noise hazards occur.
Variable Noise Attenuation: Level-dependent earmuffs are designed to provide different levels of noise attenuation based on the ambient noise level. They typically allow for communication and situational awareness in quiet environments and increase attenuation as noise levels rise.
Safety and Audibility of Warnings: EN 352-4 addresses the safety aspect of level-dependent technology, ensuring that warning signals and critical sounds can still be heard by the wearer when needed. This is crucial in occupational settings where alarms and warnings are essential for safety.
Durability: The standard specifies durability requirements for level-dependent earmuffs, ensuring that they can withstand normal wear and tear in various environments.
Marking and Labeling: Earmuffs that conform to EN 352-4 must be marked and labeled appropriately to indicate their compliance with the standard. This includes information such as the manufacturer’s name, model number, and noise reduction rating.
Testing Procedures: Manufacturers of level-dependent earmuffs must conduct tests as outlined in the standard to assess the performance of the devices. These tests typically include measuring the earmuffs’ noise reduction capabilities and verifying their ability to maintain situational awareness.
EN 352-4 is essential for industries and applications where workers need to protect their hearing while remaining aware of their surroundings or communicating with others. Level-dependent earmuffs offer a valuable solution in these situations by allowing for a balance between noise protection and situational awareness. Compliance with EN 352-4 ensures that level-dependent earmuffs meet safety and performance standards to provide effective hearing protection in challenging work environments.
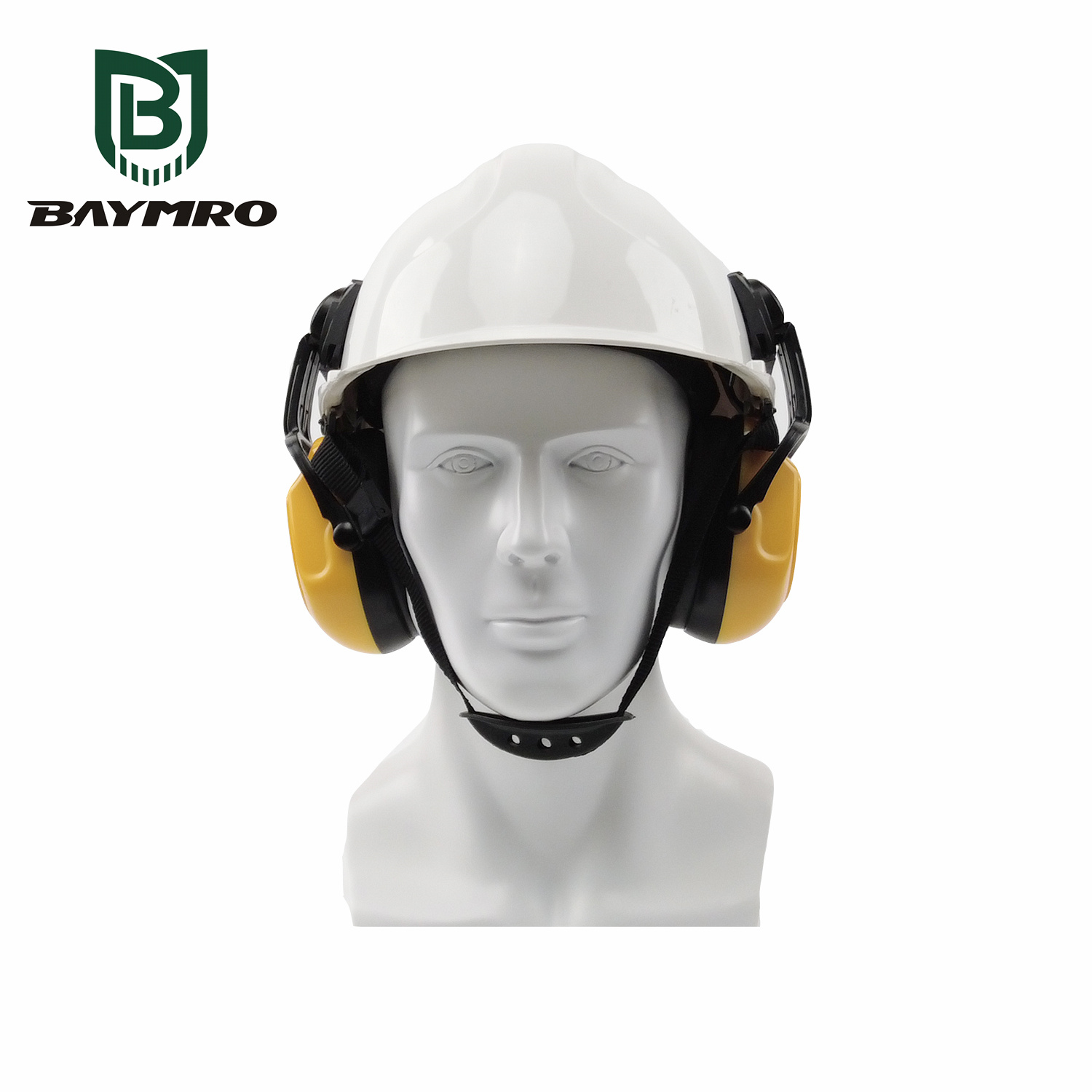
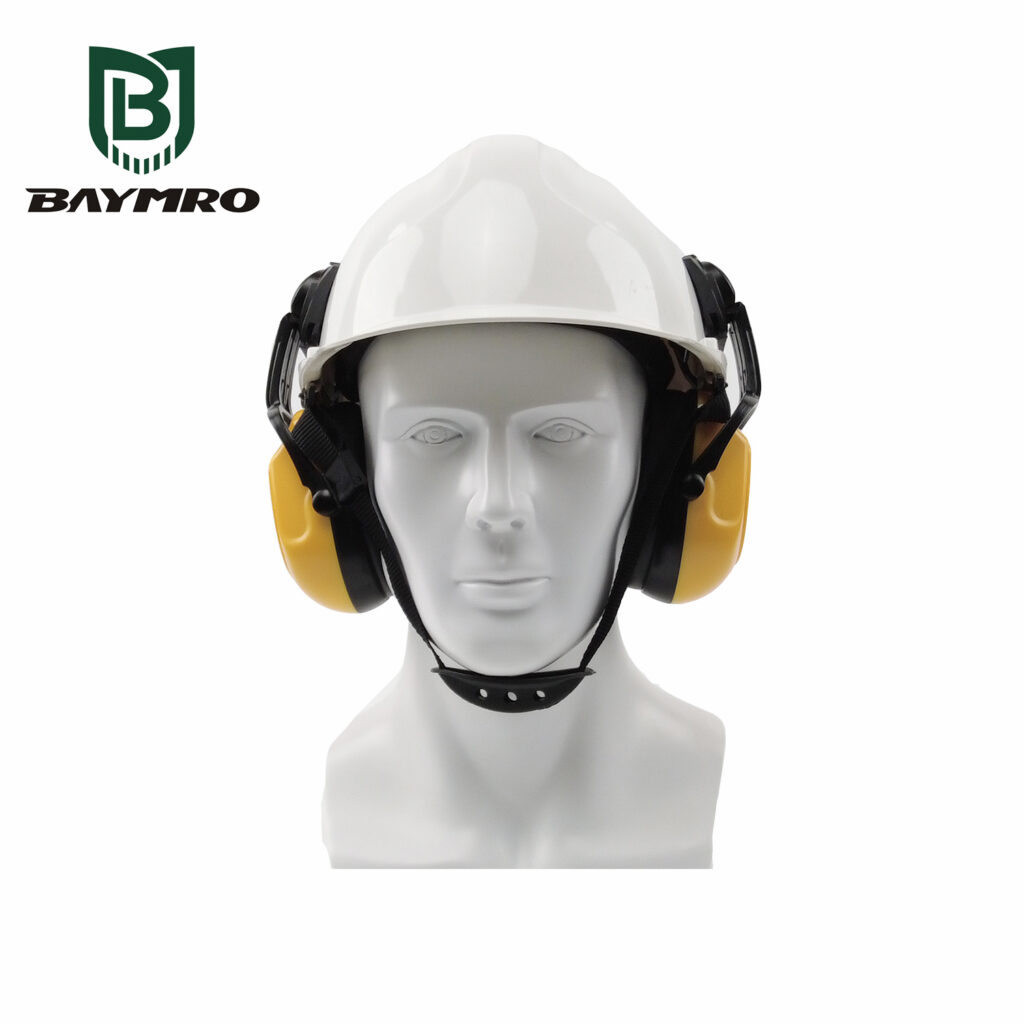
EN 352-3 is a European standard that specifically addresses ear muffs fitted to safety helmets. This standard provides requirements and testing methods for earmuffs that are integrated into industrial safety helmets, offering both hearing protection and head protection in one device. These integrated systems are commonly used in industrial and construction environments where workers are exposed to both high noise levels and potential head injury risks. Here are the key aspects of EN 352-3 for ear muffs fitted to safety helmets:
Combined Hearing and Head Protection: EN 352-3 focuses on the integration of earmuffs into industrial safety helmets, providing a comprehensive solution for workers. This combination enhances workplace safety by addressing both noise exposure and the risk of head injuries.
Noise Reduction Rating (NRR): The standard specifies minimum requirements for the noise reduction performance of the integrated earmuffs. The NRR indicates how effectively the earmuffs reduce the intensity of noise reaching the wearer’s ears. A higher NRR signifies better noise reduction capabilities.
Helmet Compatibility: EN 352-3 outlines requirements for the attachment of earmuffs to the industrial safety helmet. Ensuring compatibility with the helmet is critical to maintaining a secure and stable fit during use.
Clamping Force: The standard includes requirements for the clamping force exerted by the earmuffs on the wearer’s head. This is essential to ensure that the pressure remains within safe and comfortable limits.
Durability: EN 352-3 specifies durability requirements for the integrated system, ensuring that it can withstand the demands and conditions of the work environment.
Marking and Labeling: Earmuffs attached to safety helmets that meet EN 352-3 must be appropriately marked and labeled to indicate their compliance with the standard. This includes information such as the manufacturer’s name, model number, and noise reduction rating.
Testing Procedures: Manufacturers of ear muffs fitted to safety helmets must conduct tests as per the standard’s requirements to assess the performance of the integrated device. These tests typically include measuring noise reduction capabilities, clamping force, and durability.
EN 352-3 is particularly important in industries where both hearing protection and head protection are critical, such as construction, manufacturing, and heavy industry. By combining these two forms of protection into a single integrated system, workers can benefit from increased safety and convenience while adhering to safety and performance standards. This standard helps ensure that the integrated earmuffs and safety helmets effectively protect workers in challenging and noisy work environments.
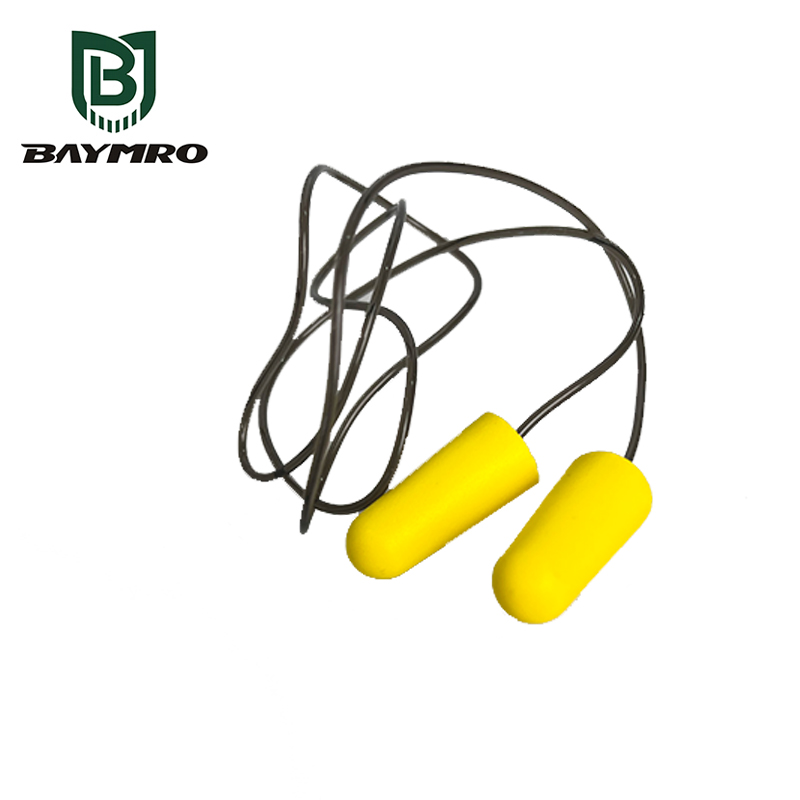
EN 352 is a series of European standards that covers various types of hearing protection devices, including earplugs. These standards specify requirements and testing methods to ensure the effectiveness and safety of hearing protection products. When it comes to earplugs, several parts of the EN 352 series are relevant:
EN 352-2: Earplugs
EN 352-2 specifically addresses earplugs used as hearing protection devices. It outlines requirements and testing methods for earplugs, including aspects such as noise reduction, comfort, durability, and safety.
EN 352-7: Level-dependent Earplugs
This part of the standard focuses on level-dependent earplugs, which are designed to offer variable protection based on noise levels. They allow wearers to hear low-level sounds, such as speech or warning signals, while protecting against high-level noise. EN 352-7 sets requirements and testing methods for such devices.
EN 352-8: Entertainment Audio Earplugs
EN 352-8 is relevant for earplugs designed for recreational or entertainment purposes, such as attending concerts or nightclubs. It addresses requirements for noise reduction and sound quality while maintaining the user’s ability to enjoy music or other forms of entertainment.
Each of these standards specifies criteria related to noise reduction, frequency range, comfort, fit, clamping force, durability, and safety. Earplug manufacturers must conform to these standards to ensure that their products provide effective hearing protection and meet safety requirements.
When selecting earplugs for hearing protection, it’s essential to consider the specific requirements of your environment and the level of noise reduction needed. Always choose earplugs that comply with the relevant EN 352 standard and follow the manufacturer’s instructions for proper fitting and use to ensure optimal protection for your hearing.

EN 352-1 does not specifically address “soundproof” earmuffs; instead, it focuses on the requirements and testing methods for hearing protection earmuffs. Earmuffs designed for hearing protection are intended to reduce the intensity of external noise reaching the wearer’s ears, but they are not typically described as “soundproof” in the sense of completely blocking out all sound.
Here’s what earmuffs designed according to EN 352-1 generally provide:
Noise Reduction: Earmuffs compliant with EN 352-1 are designed to reduce the level of external noise reaching the ears. The extent of noise reduction depends on factors such as the design of the earmuffs, the materials used, and their fit on the wearer’s head.
Comfort and Fit: EN 352-1 includes requirements for comfort and proper fit to ensure that earmuffs are comfortable for extended use and provide a good seal around the ears. Proper fit is essential for effective noise reduction.
Safety: These earmuffs are designed with safety in mind, and the standard includes requirements for clamping force to ensure that the pressure exerted on the wearer’s head is within safe limits.
Durability: Earmuffs must meet durability requirements to withstand normal wear and tear in various environments, including industrial and occupational settings.
Testing: Manufacturers of earmuffs must conduct tests according to the standard to verify the product’s performance, including its noise reduction capabilities.
While earmuffs designed to EN 352-1 specifications are effective at reducing noise levels and protecting hearing, they are not designed to create complete silence or a “soundproof” environment. The degree of noise reduction achieved depends on various factors, including the earmuff’s design, the quality of materials used, and how well they fit the wearer.
If you are looking for a product that provides a high level of soundproofing or noise isolation, you may need to consider specialized equipment such as noise-canceling headphones or custom-made hearing protection solutions. These products may not necessarily conform to EN 352-1 but are designed to block out or reduce external sounds significantly, often using active noise-canceling technology.
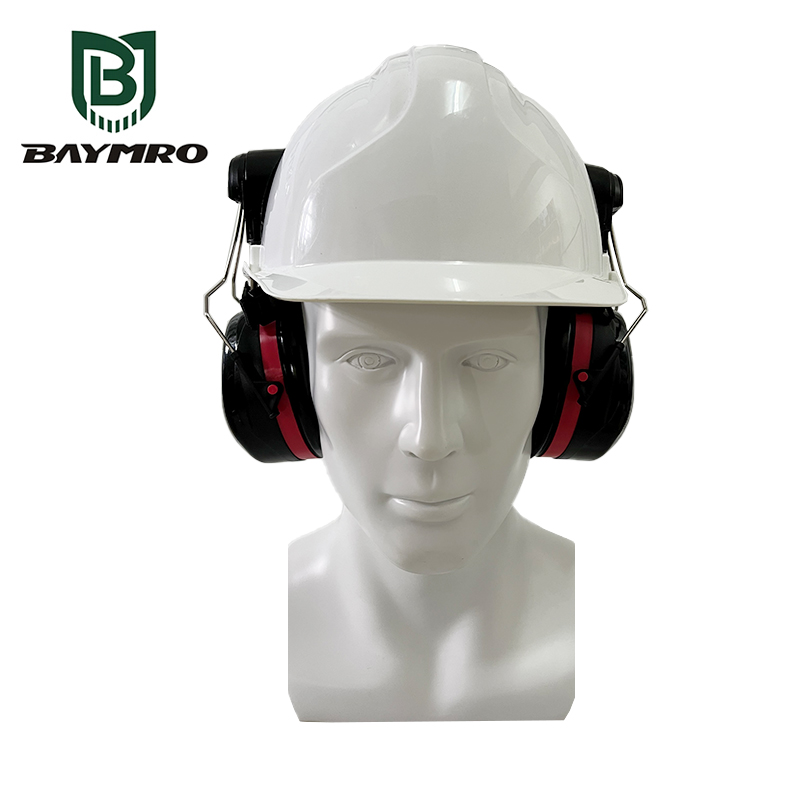
EN 352 is a set of European standards that specify requirements and testing methods for various types of hearing protection devices (HPDs) used in occupational and recreational settings. These standards are designed to ensure the effectiveness and safety of hearing protection products and to provide a common framework for manufacturers, regulatory bodies, and users across Europe. EN 352 standards cover a range of hearing protection devices, including earplugs, earmuffs, and ear canal caps.
Here is an overview of some key aspects of EN 352:
EN 352-1: Earmuffs
This part of the standard covers the requirements for earmuffs. It specifies criteria for noise reduction, comfort, and durability. Earmuffs are typically designed to cover the entire ear and are held in place by a headband.
EN 352-2: Earplugs
EN 352-2 outlines the requirements for earplugs, which are small devices designed to be inserted into the ear canal. This standard addresses aspects such as noise reduction, fit, and comfort.
EN 352-3: Earmuffs attached to an industrial safety helmet
This part of the standard focuses on earmuffs that are integrated into industrial safety helmets. It defines requirements for the combination of hearing protection and head protection.
EN 352-4: Level-dependent earmuffs
Level-dependent earmuffs are designed to protect the user from high-level noise while allowing them to hear lower-level sounds, such as speech or warning signals. This standard sets requirements and performance criteria for such devices.
EN 352-5: Active noise reduction earmuffs
Active noise reduction (ANR) earmuffs use electronic technology to cancel out or reduce noise. EN 352-5 specifies requirements and test methods for ANR earmuffs.
EN 352-6: Earmuffs with electrical audio input
Earmuffs with electrical audio input allow users to listen to external audio sources while providing hearing protection. This standard outlines requirements and testing procedures for these devices.
EN 352-7: Level-dependent earplugs
Similar to level-dependent earmuffs, level-dependent earplugs offer variable protection based on noise levels. EN 352-7 covers the requirements and testing methods for these types of earplugs.
EN 352-8: Entertainment audio earplugs
This standard is for earplugs designed for recreational or entertainment purposes, such as concerts or clubbing. It addresses requirements for noise reduction and sound quality.
EN 352-9: Earmuffs with active noise reduction
EN 352-9 focuses on earmuffs equipped with active noise reduction technology and specifies requirements for these products.
It’s essential for manufacturers to conform to these standards when designing and producing hearing protection devices. Additionally, employers and users should select and use hearing protection that complies with these standards to ensure the safety and effectiveness of the hearing protection measures in various noisy environments. Always follow the manufacturer’s instructions for proper fitting and usage of hearing protection devices to protect your hearing effectively.
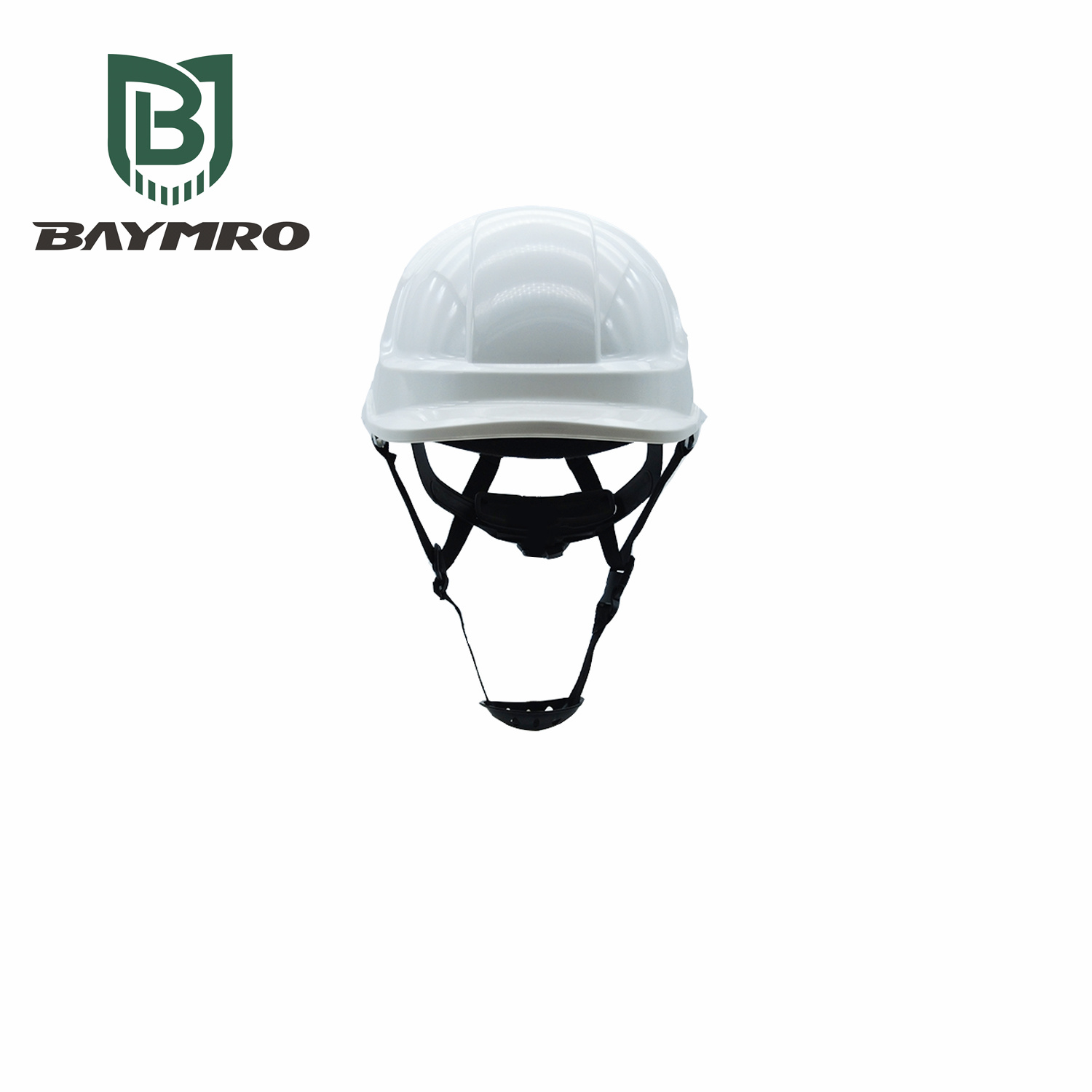
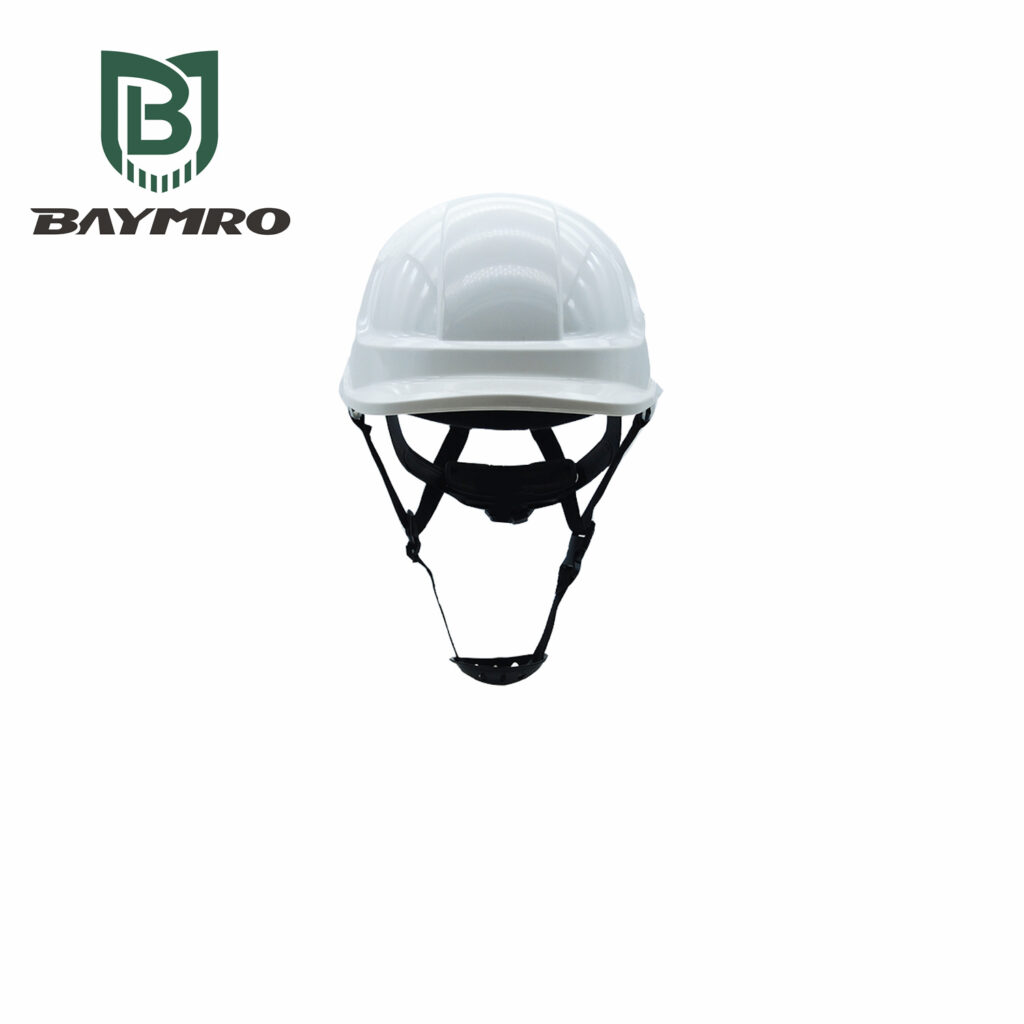
In the world of workplace safety, the protection of the head is paramount. When it comes to safeguarding the heads of workers from a myriad of occupational hazards, ANSI Z89.1 stands as a beacon of safety standards. ANSI Z89.1, developed by the American National Standards Institute (ANSI), is a critical standard that sets the requirements for industrial head protection, specifically hard hats and safety helmets. In this article, we will explore the significance of ANSI Z89.1 and its role in ensuring workplace safety.
1. Purpose and Scope
ANSI Z89.1 is a comprehensive standard that focuses on head protection equipment used in various industries and occupational settings. The primary purpose of this standard is to establish a consistent framework for the design, testing, and performance of hard hats and safety helmets. These protective helmets are essential for safeguarding the heads of workers in environments where head injuries may occur due to falling objects, impact, electrical hazards, or other potential dangers.
2. Types of Protection
ANSI Z89.1 covers a wide range of protective headgear, including:
Type I Helmets: Designed to provide protection to the top of the head, they are commonly used in situations where falling objects are a risk.
Type II Helmets: Offering protection both to the top and sides of the head, they are suitable for environments where lateral impact is a concern.
3. Design Requirements
The standard outlines stringent design requirements for hard hats and safety helmets. These requirements ensure that the headgear provides effective protection while also being comfortable and practical for extended wear. Design factors include impact resistance, shock absorption, electrical insulation, and suspension systems.
4. Testing Procedures
Helmets that comply with ANSI Z89.1 must undergo rigorous testing procedures to verify their compliance with the standard. These tests evaluate various aspects of performance, including impact resistance, electrical insulation properties, and suspension system effectiveness.
5. Marking and Labeling
Products that meet the ANSI Z89.1 standard are marked and labeled accordingly. These markings include information about the manufacturer, product model, and compliance with the standard. Users can refer to these markings to ensure they are selecting suitable headgear for their specific workplace needs.
6. Workplace Safety
ANSI Z89.1 compliant hard hats and safety helmets are essential for maintaining workplace safety in various industries, including construction, manufacturing, and utilities. Employers are often required to provide and enforce the use of ANSI-compliant head protection to reduce the risk of head injuries in hazardous work environments.
7. Compatibility
ANSI Z89.1 is compatible with other workplace safety standards and regulations, ensuring that head protection can be integrated seamlessly into broader safety protocols and personal protective equipment (PPE) requirements.
In summary, ANSI Z89.1 is a critical American standard that sets the benchmark for the design, testing, and performance of hard hats and safety helmets used in a variety of work environments. Compliance with this standard is essential for ensuring the safety and well-being of workers who face the risk of head injuries due to occupational hazards. ANSI Z89.1 underscores the importance of comprehensive safety measures in the workplace and serves as a vital component of occupational safety and health programs.
221028-White-safety-helmet-Model-.jpg)
In the world of electrical work, safety is paramount. When dealing with live electrical installations or working in close proximity to live parts, the risk of electrocution is a constant concern. To mitigate this danger, the European standard EN 50365 plays a crucial role by specifying the requirements for electrically insulating helmets. These helmets are designed to safeguard workers by preventing electrical currents from passing through the human body via the head. In this article, we will delve into the importance and significance of EN 50365.
1. Protection Against Electrocution
EN 50365 is a European standard that focuses on electrically insulating helmets used in scenarios where working on live electrical installations or close to live parts is necessary. These helmets are not ordinary headgear; they are specifically designed to protect workers from electrocution, a potentially fatal hazard associated with electrical work.
2. Key Purpose
The primary purpose of EN 50365 compliant electrically insulating helmets is to provide a barrier between the wearer’s head and live electrical parts. These helmets are dielectric, meaning they do not conduct electricity. When properly used in conjunction with other insulating equipment, such as gloves and footwear, they effectively prevent electrical currents from passing through the body via the head, ensuring the safety of the wearer.
3. Design Requirements and Testing
EN 50365 specifies rigorous design requirements that electrically insulating helmets must meet to be compliant. These requirements ensure that the helmets provide adequate electrical insulation while also being comfortable and practical for wear during electrical work. Helmets must pass stringent testing procedures to verify their compliance, including assessments of their dielectric strength and insulation properties.
4. Workplace Safety
Electricians, utility workers, and other professionals in the electrical field rely on EN 50365 compliant helmets to protect themselves from potentially lethal electrical hazards. Employers are often mandated to provide and enforce the use of these specialized helmets to safeguard their workers and maintain workplace safety.
5. Complementary Protection
EN 50365 helmets are typically used in combination with other personal protective equipment (PPE), such as insulating gloves and footwear. This comprehensive approach to safety ensures that electrical workers have multiple layers of protection against electric shock.
6. Compatibility and European Regulation
EN 50365 aligns with European workplace safety standards and regulations, contributing to a cohesive safety framework across European industries. This compatibility allows for the integration of electrically insulating helmets into broader safety protocols and PPE requirements.
In summary, EN 50365 is a vital European standard that addresses a critical need for safety in electrical work environments. By specifying the requirements for electrically insulating helmets, it helps protect the lives of workers who face the ever-present risk of electrocution. Compliance with EN 50365 is essential for ensuring the safety and well-being of individuals working with live electrical installations, and it underscores the importance of comprehensive safety measures in electrical professions.
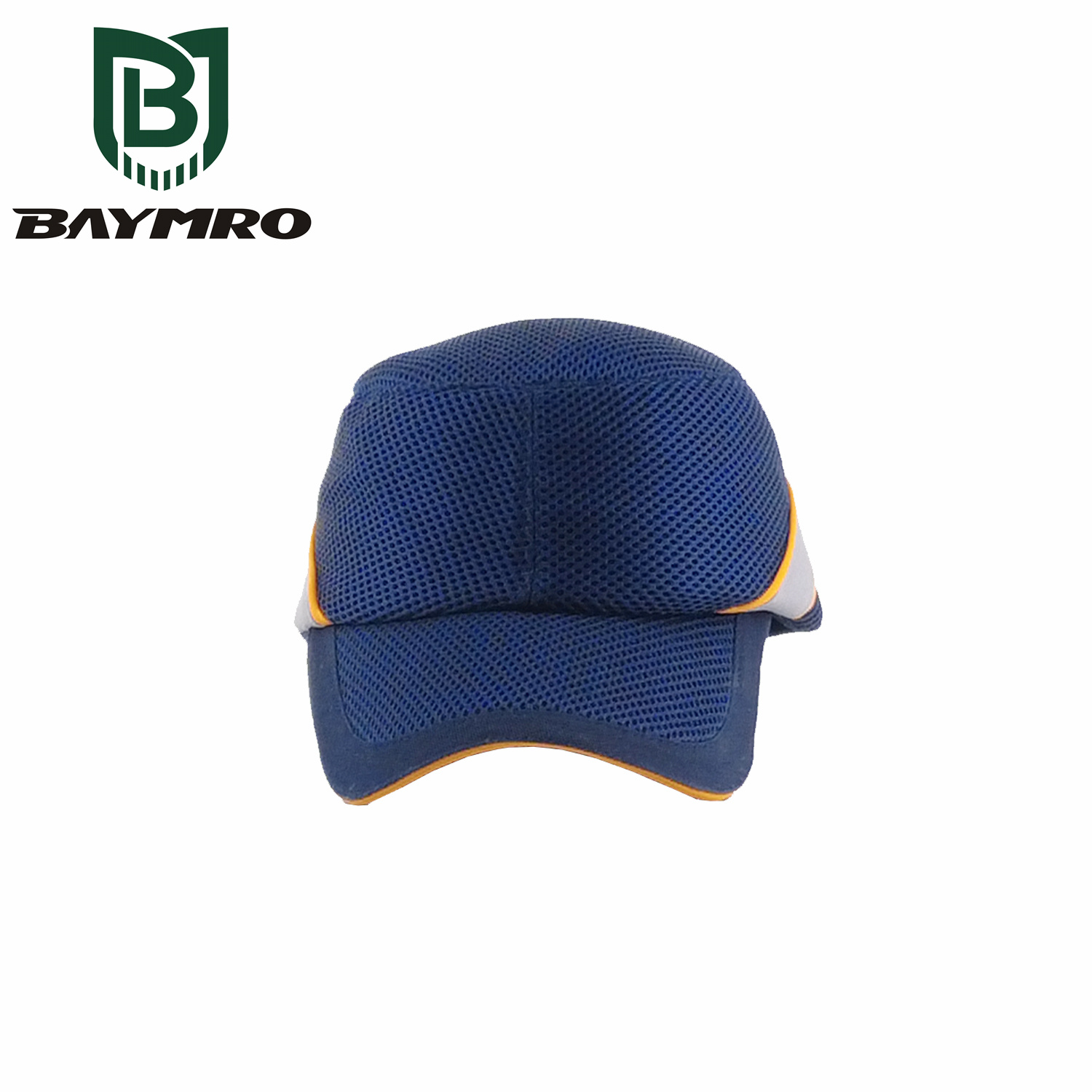
EN 812 is a European standard that specifies the requirements and testing methods for industrial bump caps. These caps are designed to provide protection to workers against minor head bumps and impacts in various industrial and occupational settings. EN 812 sets the criteria for design, performance, and testing of these protective headwear items. Here’s an overview of EN 812:
1. Purpose and Scope
EN 812 primarily focuses on bump caps used in workplaces where there is a risk of minor head injuries due to low-level impacts. Unlike full-scale safety helmets (which meet different standards), bump caps are designed for protection against minor bumps and scrapes rather than severe head injuries.
2. Types of Protection
Bump caps are intended to safeguard the head from low-velocity impacts and minor head injuries caused by falling objects, bumping into stationary objects, or other similar situations. They provide a level of protection between standard headgear and no protection at all.
3. Design Requirements
EN 812 outlines design requirements for industrial bump caps, ensuring they provide reasonable protection while being comfortable and practical for wear in various work environments. These requirements cover factors such as impact resistance, weight, and ventilation.
4. Testing Procedures
Bump caps that conform to EN 812 must undergo testing to verify their compliance with the standard. These tests evaluate various aspects of performance, including impact resistance, penetration resistance, and the structural integrity of the cap.
5. Marking and Labeling
Products that meet the EN 812 standard must be marked and labeled accordingly. These markings typically include information about the manufacturer, product model, and compliance with the standard. These markings help users identify suitable headgear that provides a certain level of protection against minor impacts.
6. Workplace Safety
Compliance with EN 812 is important for maintaining workplace safety, especially in industries and occupations where there is a risk of minor head injuries. Employers often require the use of EN 812 compliant bump caps to reduce the risk of head injuries in these settings.
7. Compatibility
EN 812 can be used in conjunction with other workplace safety standards, such as those for eye protection or hearing protection, to ensure comprehensive protection for workers in various hazardous work environments.
In summary, EN 812 is a European standard that sets the requirements for industrial bump caps used in workplaces where there is a potential risk of minor head injuries due to low-level impacts. Compliance with this standard helps mitigate the risk of minor head injuries, promoting a safer work environment in Europe. Employers and users should ensure that the bump caps they use meet EN 812 standards to enhance safety and reduce the risk of minor head injuries on the job.
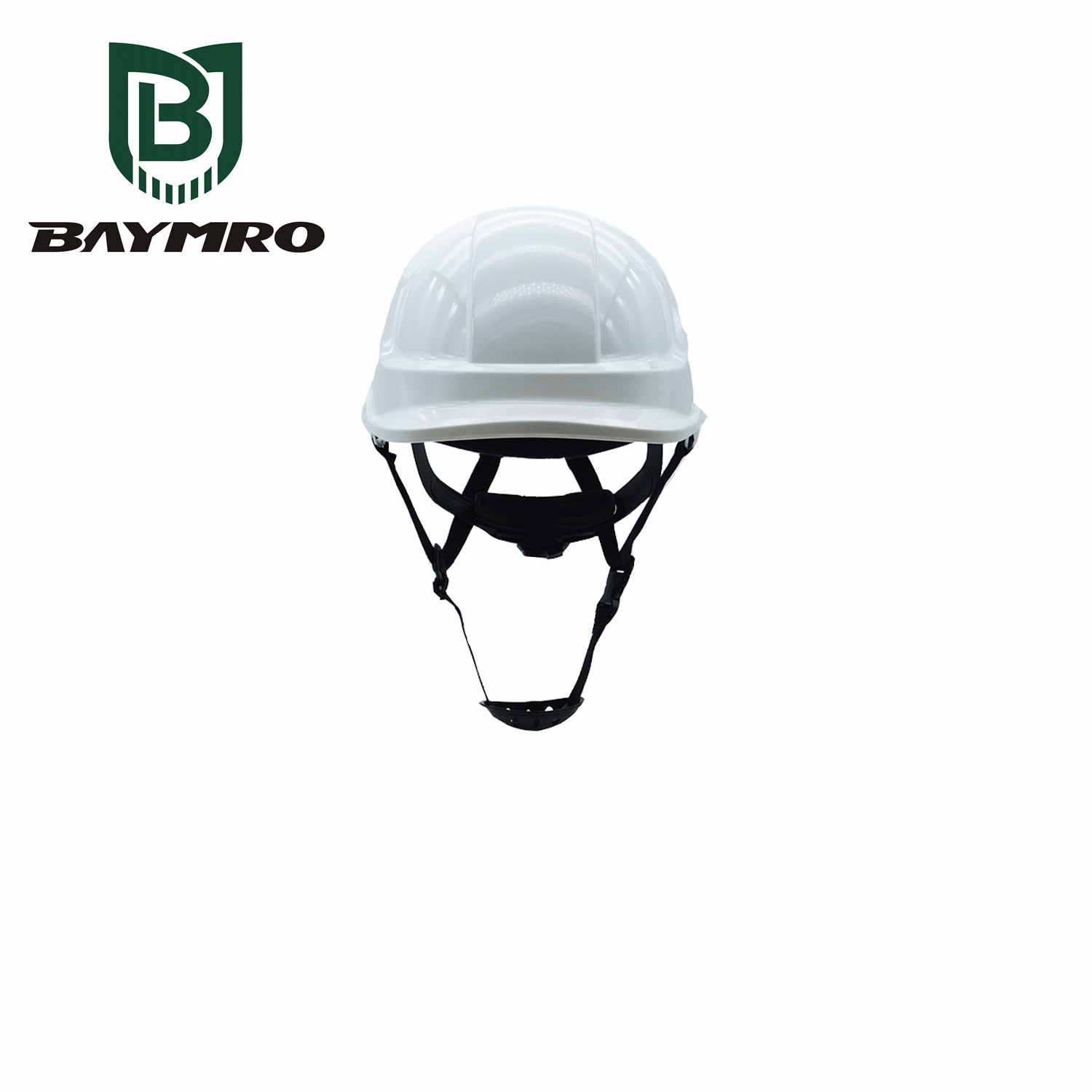
EN 397 is a European standard that sets forth the specifications and requirements for industrial safety helmets. These helmets are essential protective gear designed to safeguard the heads of workers in various industrial and occupational settings across Europe. EN 397 ensures that safety helmets meet stringent criteria for design, testing, and performance. Here’s an overview of EN 397:
1. Purpose and Scope
EN 397 primarily focuses on safety helmets used to protect the heads of individuals working in industries and occupations where head injuries may occur. The standard aims to establish a consistent framework for the design, testing, and performance of industrial safety helmets.
2. Types of Protection
This standard covers a range of protective headgear, including hard hats and safety helmets. These helmets are designed to safeguard the head against different types of risks commonly encountered in industrial, construction, and similar work environments.
3. Design Requirements
EN 397 outlines design requirements for industrial safety helmets, ensuring they provide comprehensive protection while also being comfortable and user-friendly. These requirements encompass factors such as impact resistance, shock absorption, and chin strap performance.
4. Testing Procedures
Safety helmets that comply with EN 397 must undergo rigorous testing procedures to verify their compliance with the standard. These tests evaluate various aspects of performance, including impact resistance, penetration resistance, and resistance to flame.
5. Marking and Labeling
Products that meet the EN 397 standard must be marked and labeled accordingly. These markings typically include information about the manufacturer, product model, and compliance with the standard. Such markings help users identify suitable headgear for their specific needs.
6. Workplace Safety
Compliance with EN 397 is essential for maintaining workplace safety in Europe. Employers are often required to provide and enforce the use of EN 397 compliant safety helmets to reduce the risk of head injuries in hazardous work environments.
7. Compatibility
EN 397 is compatible with other European workplace safety standards, allowing for a comprehensive approach to employee protection. This compatibility ensures that various aspects of safety gear, such as eye protection, respiratory protection, and hearing protection, can work together effectively to enhance overall workplace safety.
In summary, EN 397 is a critical European standard that sets the requirements for industrial safety helmets used in a variety of work environments. Compliance with this standard helps mitigate the risk of head injuries and promotes a safer and healthier workplace in Europe. Users and employers should ensure that the headgear they use meets EN 397 standards to enhance safety and reduce the risk of accidents and injuries on the job.