Archive for the ‘Certification’ Category
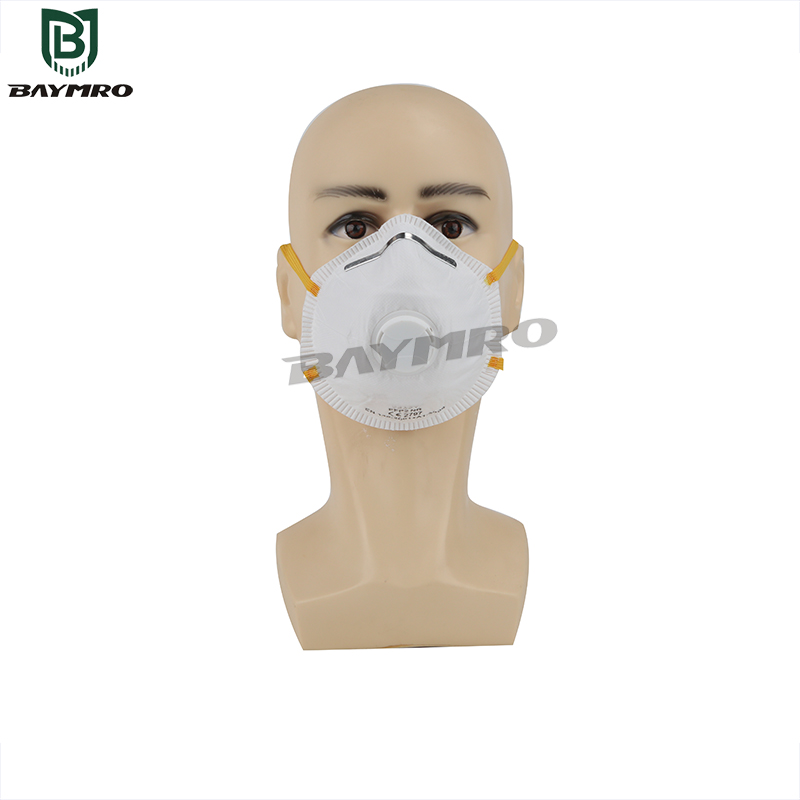
In any occupational setting where respiratory hazards pose a threat, selecting the appropriate respiratory protection products is paramount to ensuring the health and safety of workers. Here’s a structured approach to guide the selection process:
- Assess the Environment:
Begin by conducting a thorough assessment of the workplace environment. Identify potential respiratory hazards such as dust, smoke, gases, vapors, and other airborne contaminants. - Determine Risk Levels:
Evaluate the level of risk associated with each identified hazard. Consider factors such as the nature of the hazards, their concentration levels, and the duration of exposure. - Calculate Concentration Levels:
Utilize appropriate measurement devices to quantify the concentration levels of hazardous substances in the air. This step is crucial in determining the appropriate respiratory protection products and protection levels needed. - Select Suitable Respiratory Protection Products:
Based on the calculated concentration levels, risk assessment, and environmental characteristics, choose the most suitable respiratory protection products. Options may include filtering facepiece respirators (FFRs), half-face masks, full-face masks, powered air-purifying respirators (PAPRs), or supplied-air respirators (SARs). - Verify Compliance and Certification:
Ensure that the selected respiratory protection products comply with relevant standards and regulations. Look for certifications such as NIOSH (National Institute for Occupational Safety and Health) in the United States, EN (European Norms) in Europe, or ISO (International Organization for Standardization) certifications. - Provide Training and Guidance:
Offer comprehensive training and guidance to workers on the proper selection, fitting, use, and maintenance of respiratory protection products. Ensure that employees understand how to wear and adjust the products correctly to ensure their effectiveness and protection. - Regular Evaluation and Updating:
Regularly assess the performance and condition of respiratory protection products. Update and replace products as needed to maintain their effectiveness and reliability. Adjust product selection and usage based on changes in the workplace environment and employee needs.
By following this structured approach, organizations can effectively select and deploy the right respiratory protection products to mitigate respiratory hazards and protect the health and safety of their workforce. This systematic process ensures compliance with regulations, enhances workplace safety, and promotes a culture of health and well-being.
EN149 Respiratory Protective Devices: Ensuring Respiratory Safety in Hazardous Environments
2024
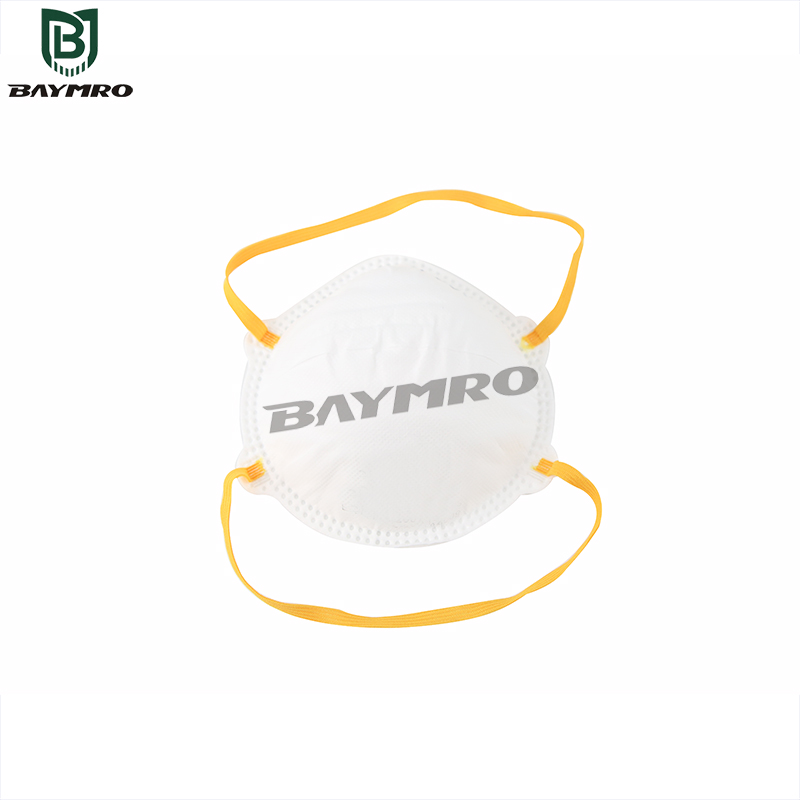
In hazardous work environments where airborne contaminants pose a threat to respiratory health, EN149 Respiratory Protective Devices play a pivotal role in safeguarding workers against the inhalation of harmful substances. This article provides an overview of EN149 standards, outlining their significance, classification, and application in ensuring respiratory safety.
Significance of EN149 Standards
EN149 standards, established by the European Committee for Standardization (CEN), define the requirements and testing procedures for filtering half masks used as respiratory protective devices. These standards ensure that respiratory protective devices meet stringent criteria for filtration efficiency, breathing resistance, fit, and comfort, thereby providing effective protection against airborne particles and aerosols.
By adhering to EN149 standards, manufacturers can demonstrate the quality, performance, and reliability of their respiratory protective devices, instilling confidence in users and regulatory authorities alike. Compliance with EN149 standards is essential for ensuring the safety and well-being of workers in a wide range of industries, including construction, manufacturing, healthcare, and agriculture.
Classification of EN149 Respiratory Protective Devices
EN149 classifies respiratory protective devices into three categories based on their filtration efficiency and resistance to inhalation and exhalation:
FFP1: Filtering Face Piece with a minimum filtration efficiency of 80% and a maximum inward leakage rate of 22%.
FFP2: Filtering Face Piece with a minimum filtration efficiency of 94% and a maximum inward leakage rate of 8%.
FFP3: Filtering Face Piece with a minimum filtration efficiency of 99% and a maximum inward leakage rate of 2%.
These classifications indicate the device’s ability to filter out airborne particles of varying sizes, ranging from coarse dust particles to fine aerosols.
Application of EN149 Respiratory Protective Devices
EN149 respiratory protective devices, commonly known as filtering facepieces (FFP), are designed for use in environments where workers are exposed to airborne particles, such as dust, mist, fumes, and biological agents. These devices are lightweight, compact, and easy to use, making them suitable for a wide range of applications, including construction work, mining, metalworking, healthcare, and emergency response.
Workers must select the appropriate FFP based on the level of respiratory protection required and the specific hazards present in their work environment. Proper fit testing and training are essential to ensure the effective use of EN149 respiratory protective devices and to minimize the risk of exposure to airborne contaminants.
Conclusion
In conclusion, EN149 Respiratory Protective Devices play a critical role in ensuring respiratory safety and protecting workers from airborne hazards in the workplace. By adhering to stringent standards and classification criteria, these devices provide reliable and effective protection against a wide range of airborne particles and aerosols. Employers and workers must prioritize the selection, use, and maintenance of EN149 respiratory protective devices to mitigate the risk of respiratory illness and injury and promote a culture of safety and well-being in the workplace.
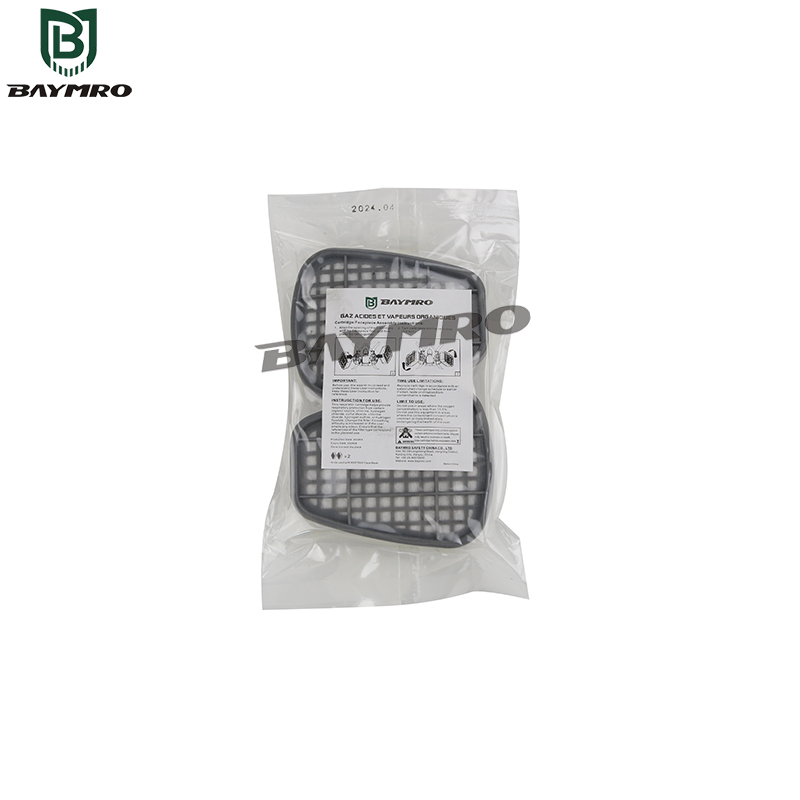
In environments where airborne particulate matter poses a risk to respiratory health, EN143 Particulate Filter Cartridges serve as indispensable components of respiratory protective equipment (RPE), providing essential protection against dust, fumes, mist, and other airborne particles. This article explores the function, classification, and applications of EN143 particulate filters, highlighting their importance in safeguarding worker health and promoting workplace safety.
Function and Classification
EN143 establishes the requirements and testing procedures for particulate filter cartridges used in respiratory protective devices. Particulate filters are designed to capture airborne particles, preventing their entry into the respiratory system and reducing the risk of respiratory illness and injury.
Particulate filter cartridges are classified into three categories based on their filtration efficiency and resistance to oil:
P1: Low-efficiency filters with a minimum filtration efficiency of 80%.
P2: Medium-efficiency filters with a minimum filtration efficiency of 94%.
P3: High-efficiency filters with a minimum filtration efficiency of 99.95%.
These classifications indicate the filter’s ability to remove particles of varying sizes, ranging from coarse dust particles to fine particulate matter.
Applications and Usage
EN143 particulate filter cartridges find application in a wide range of industries and work environments where workers are exposed to airborne particles, including construction, mining, manufacturing, agriculture, healthcare, and more. These filters are commonly used in conjunction with respiratory protective devices such as half-masks, full-face masks, powered air-purifying respirators (PAPRs), and self-contained breathing apparatus (SCBA), providing essential respiratory protection to workers in hazardous environments.
Workers must select the appropriate particulate filter cartridge based on the specific hazards present in their work environment, including the type and concentration of airborne particles. Regular inspection and replacement of filters are essential to ensure continued effectiveness and optimal protection against respiratory hazards. Employers should provide comprehensive training on filter selection, usage, and maintenance to ensure the safety and well-being of their workers.
Compliance and Certification
EN143 particulate filter cartridges undergo rigorous testing to evaluate their performance, including filtration efficiency, breathing resistance, and particle loading capacity. Filters that meet the requirements of EN143 are marked with the CE (Conformité Européenne) certification, indicating compliance with European Union regulations for PPE.
Employers should ensure that particulate filter cartridges are compatible with the respiratory protective devices used in their workplace and provide workers with appropriate training and guidance on their selection and usage. Regular monitoring of workplace air quality, coupled with proper maintenance of respiratory protective equipment, is essential to mitigate the risk of exposure to airborne particles and safeguard worker health and safety.
Conclusion
In conclusion, EN143 Particulate Filter Cartridges play a critical role in protecting workers from the harmful effects of airborne particles in the workplace. By adhering to stringent standards and certification requirements, these filters ensure reliable and effective respiratory protection, enabling workers to perform their duties safely and confidently in challenging environments. Employers and workers alike must prioritize the selection, usage, and maintenance of respiratory protective equipment to minimize the risk of respiratory hazards and promote a culture of safety and well-being in the workplace.
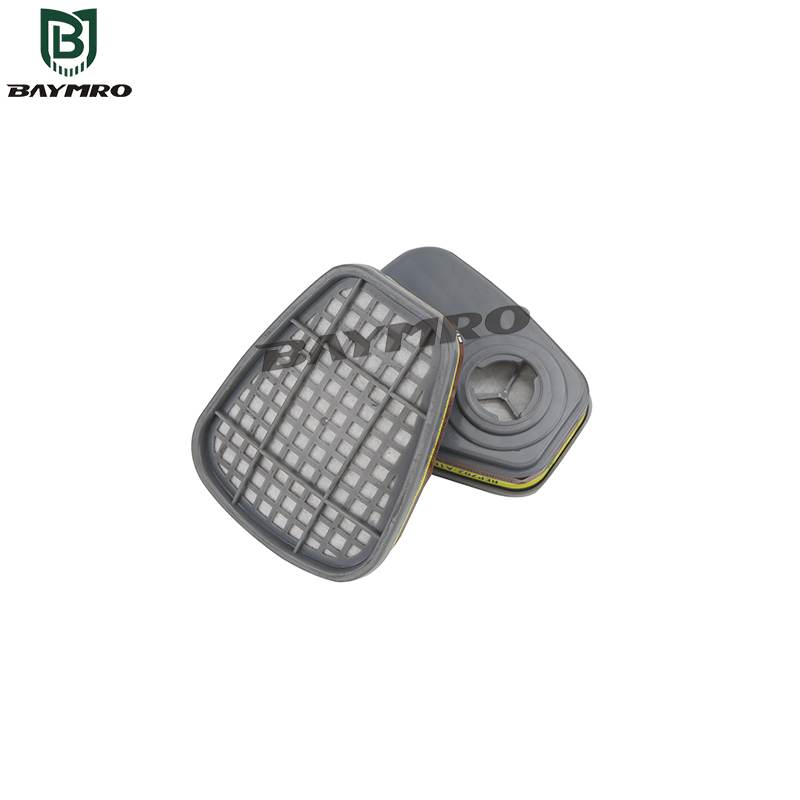
In environments where hazardous gases pose a threat to respiratory health, EN14387 Gas Filters and Combination Filters emerge as critical components of personal protective equipment (PPE), providing essential protection against a wide range of airborne contaminants. This article examines the functionality, classification, and applications of EN14387 filters, emphasizing their role in ensuring worker safety and well-being.
Functionality and Classification
EN14387 establishes the requirements and testing procedures for gas filters and combination filters used in respiratory protective devices. Gas filters are designed to remove specific gases or vapors from the air, while combination filters integrate both gas and particulate filtration capabilities, offering comprehensive protection against multiple hazards.
Gas filters are classified into four categories based on their capacity to adsorb specific gases:
Type A: For organic gases and vapors with a boiling point above 65°C.
Type B: For inorganic gases and vapors, excluding carbon monoxide (CO).
Type E: For sulfur dioxide (SO2) and acidic gases and vapors.
Type K: For ammonia (NH3) and organic ammonia derivatives.
Combination filters are denoted by a combination of letters representing the gases and vapors they can adsorb. For example, an ABEK filter can adsorb organic gases and vapors (A), inorganic gases and vapors (B), acidic gases and vapors (E), and ammonia and organic ammonia derivatives (K).
Applications and Usage
EN14387 filters find application across various industries where workers are exposed to hazardous gases and vapors, including chemical manufacturing, petrochemical refining, pharmaceuticals, and agriculture. These filters are commonly used in conjunction with respiratory protective devices such as half-masks, full-face masks, and powered air-purifying respirators (PAPRs), providing essential protection to workers in potentially hazardous environments.
Workers must select the appropriate filter type and class based on the specific gases and vapors present in their work environment. Regular inspection and replacement of filters are essential to ensure continued effectiveness and optimal protection against respiratory hazards. Employers should provide comprehensive training on filter selection, usage, and maintenance to ensure the safety and well-being of their workers.
Compliance and Certification
EN14387 filters undergo rigorous testing to evaluate their performance, including filtration efficiency, breakthrough time, and breathing resistance. Filters that meet the requirements of EN14387 are marked with the CE (Conformité Européenne) certification, indicating compliance with European Union regulations for PPE.
Employers should ensure that filters are compatible with the respiratory protective devices used in their workplace and provide workers with appropriate training and guidance on their selection and usage. Regular monitoring of workplace air quality, coupled with proper maintenance of respiratory protective equipment, is essential to mitigate the risk of exposure to hazardous gases and safeguard worker health and safety.
Conclusion
In conclusion, EN14387 Gas Filters and Combination Filters play a vital role in protecting workers from the harmful effects of hazardous gases and vapors in the workplace. By adhering to stringent standards and certification requirements, these filters ensure reliable and effective respiratory protection, enabling workers to perform their duties safely and confidently in challenging environments. Employers and workers alike must prioritize the selection, usage, and maintenance of respiratory protective equipment to minimize the risk of respiratory hazards and promote a culture of safety and well-being in the workplace.
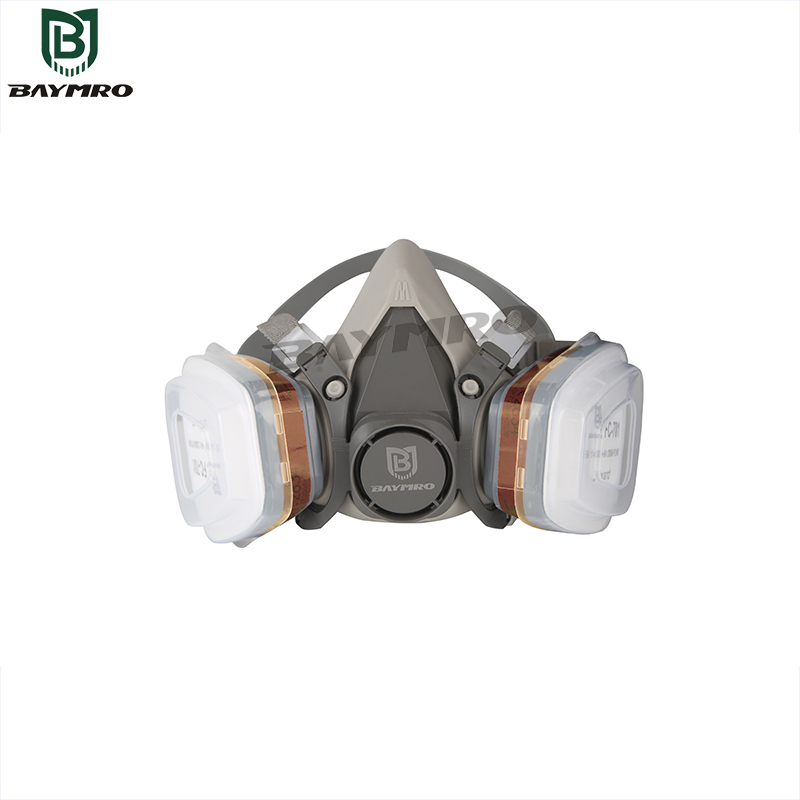
In environments where respiratory hazards are present, the EN140 respirator half mask is a reliable solution that provides basic protection while ensuring comfort and ease of use. This article explores the key features and benefits of the EN140 respirator half mask, highlighting its importance in protecting users from airborne contaminants and promoting workplace safety. Optimized design for comfort and functionality
The EN140 respirator half mask has been carefully designed to strike a balance between comfort and functionality, allowing users to perform their duties with confidence and ease. Its ergonomic design conforms to the natural contours of the face, ensuring a secure fit, minimizing leaks and maximizing protection. Made from lightweight and durable materials such as thermoplastic elastomer (TPE) or silicone, the half mask can be worn for extended periods of time without causing discomfort or fatigue. Adjustable shoulder and back straps enable users to customize the fit to their personal preferences, ensuring optimal comfort and stability over extended periods of use. Versatile protection against respiratory hazards
The EN140 respirator half mask is equipped with replaceable particle filters and/or gas/vapor cartridges to provide versatile protection against a wide range of respiratory hazards, including dust, mist, gas and vapor. The mask’s filtration system effectively removes airborne contaminants from the inhaled air, preventing them from entering the respiratory system and safeguarding the health and well-being of the user. In addition, the half mask is compatible with a wide range of filter and cartridge options, allowing users to tailor their respiratory protection to the specific hazards in their work environment. This adaptability enhances the mask’s usefulness in a variety of industries and applications, from construction and manufacturing to healthcare and agriculture. Compliance and certifications
The EN140 respirator half mask is designed and manufactured to comply with European standards for respiratory protective equipment, including EN 140:1998. This certification ensures that the mask meets stringent performance, safety and reliability standards, giving users confidence in its effectiveness and suitability for use in hazardous environments. In addition, the half mask undergoes a rigorous testing and quality assurance program to verify its compliance with regulatory requirements and industry standards. Regular inspection and maintenance practices outlined in the mask’s user manual further ensure its continued performance and durability. Conclusion
In conclusion, the EN140 respirator half mask provides a reliable and versatile solution for respiratory protection in a variety of workplace environments. With its optimized design, versatile filtering capabilities and compliance with industry standards, this half mask gives users the confidence and peace of mind to complete tasks safely and effectively. Whether in construction, manufacturing, healthcare or other industries, the EN140 respirator half mask is an indispensable tool for protecting respiratory health and promoting workplace safety.
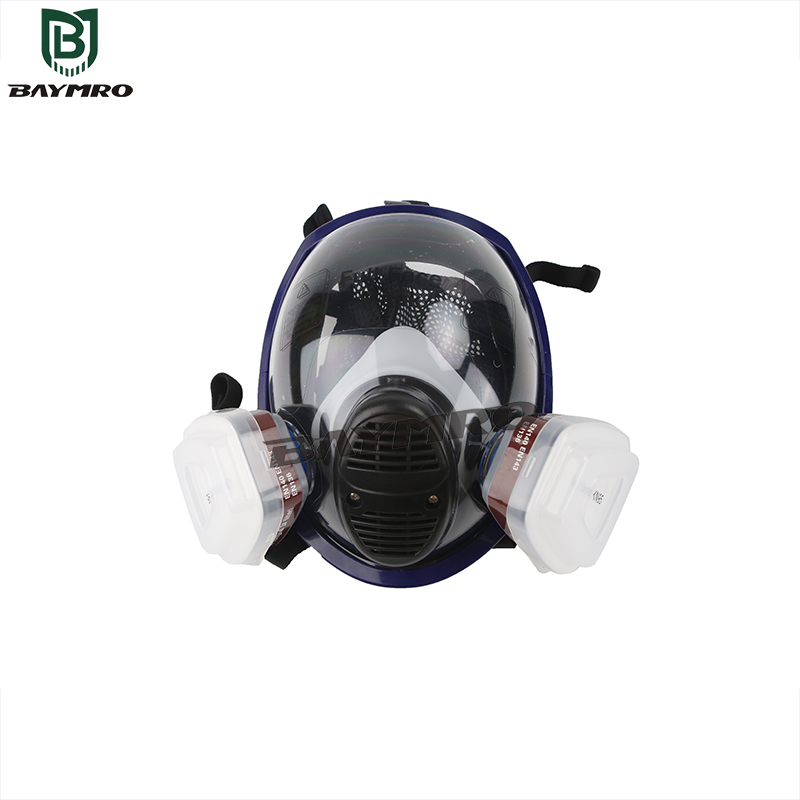
Abstract:
EN136 Full Face Respirator is a vital piece of personal protective equipment (PPE) used in various industries to safeguard workers from inhaling harmful substances. This article provides an in-depth examination of the design, functionality, and applications of the EN136 Full Face Respirator, emphasizing its role in ensuring occupational safety and health.
Introduction
The occupational exposure to hazardous chemicals, gases, and particulate matter poses significant health risks to workers across different sectors. In response to these risks, the EN136 Full Face Respirator has emerged as a crucial tool in protecting workers from inhaling contaminants present in the workplace environment.
Design and Components
The EN136 Full Face Respirator is designed to provide comprehensive protection to the wearer’s face, covering the eyes, nose, and mouth. It consists of several key components, including a transparent visor, a face seal, inhalation and exhalation valves, straps for securing the mask, and filters/cartridges for removing contaminants from the air.
Functionality
The functionality of the EN136 Full Face Respirator is centered around its ability to create a sealed barrier between the wearer’s face and the surrounding environment. The transparent visor ensures unrestricted vision while the face seal prevents leakage of contaminants into the mask. Inhalation valves allow the wearer to breathe in filtered air, while exhalation valves facilitate the effortless expulsion of exhaled breath, reducing heat and moisture buildup within the mask.
Applications
The EN136 Full Face Respirator finds application in a wide range of industries, including but not limited to chemical manufacturing, pharmaceuticals, petrochemicals, construction, and healthcare. It is particularly suited for environments where there is a risk of exposure to toxic gases, vapors, fumes, or airborne particles.
Maintenance and Care
Proper maintenance and care are essential to ensure the effectiveness of the EN136 Full Face Respirator. Regular inspection of the components, such as the visor, face seal, and valves, is necessary to detect any signs of wear or damage. Additionally, timely replacement of filters/cartridges according to manufacturer recommendations is crucial for optimal performance.
Conclusion
In conclusion, the EN136 Full Face Respirator plays a critical role in protecting workers from hazardous airborne contaminants in various industrial settings. Its robust design, functionality, and broad applicability make it an indispensable tool for ensuring occupational safety and health. However, it is imperative that users adhere to proper maintenance and care practices to maximize the lifespan and effectiveness of the respirator.
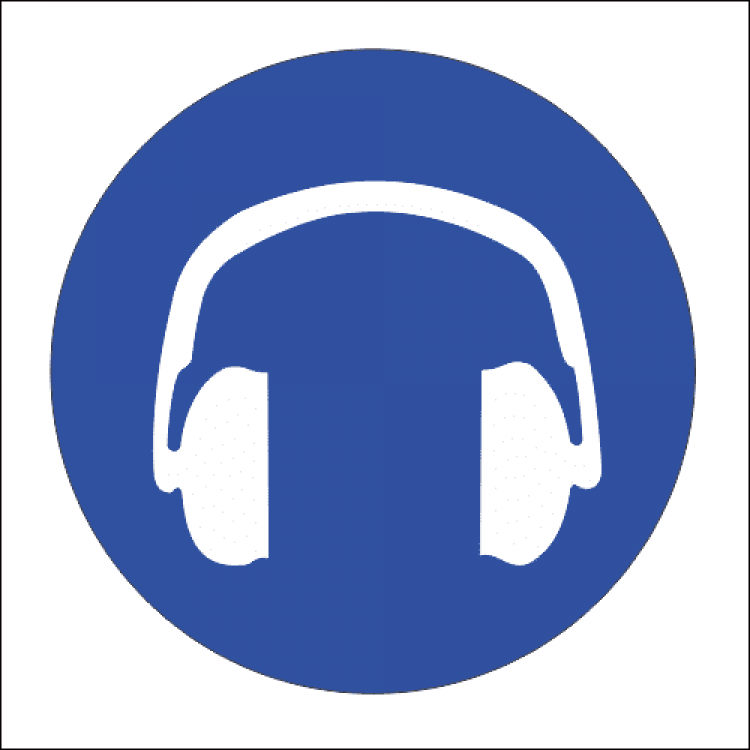
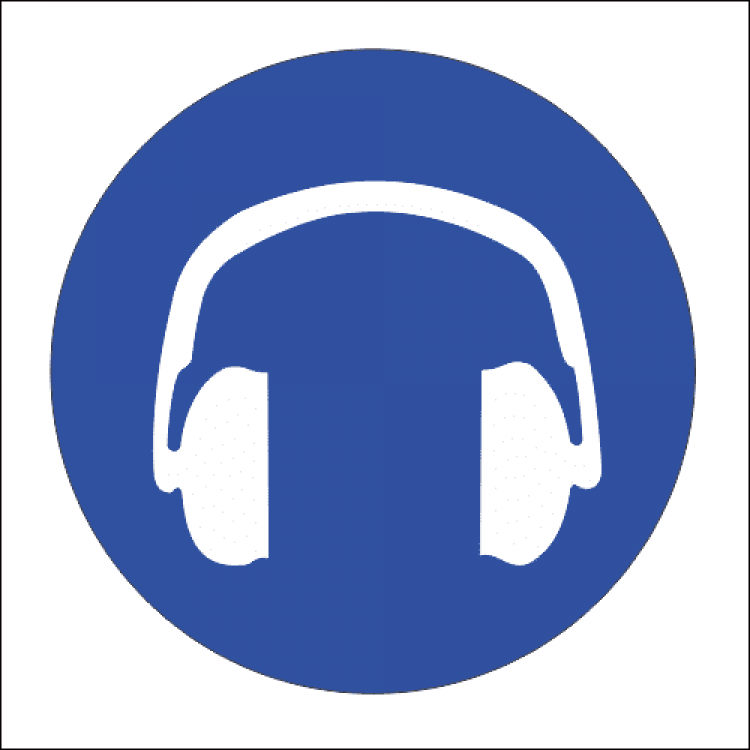
Choosing the right hearing protection products is crucial to safeguard your hearing in noisy environments. The choice depends on several factors, including the noise level, your specific needs, comfort, and the environment. Here are steps to help you select appropriate hearing protection:
Assess Noise Levels:
Determine the noise level in your workplace or environment. You may need a professional noise assessment to accurately measure sound levels. This will help you understand the level of protection required.
Understand Types of Hearing Protection:
Familiarize yourself with different types of hearing protection products:
Earplugs: Small, insertable devices that go inside the ear canal.
Earmuffs: Head-worn devices that cover the ears.
Level-Dependent Hearing Protectors: Earmuffs or earplugs that adjust protection based on noise levels.
Communication Hearing Protectors: Allow for communication while providing protection.
Consider Noise Reduction Rating (NRR):
Look for the Noise Reduction Rating (NRR) when choosing earplugs or earmuffs. The NRR indicates the level of noise reduction provided by the product. Select a product with an NRR appropriate for your noise environment.
Fit and Comfort:
Ensure a proper fit. Ill-fitting hearing protection may not provide the expected noise reduction. Try different sizes and types to find the most comfortable fit.
Comfort is essential for extended use. Choose products that you can wear comfortably throughout your work shift.
Communication Needs:
If you need to communicate while wearing hearing protection, consider products with built-in communication features or those that allow for easy removal or adjustment.
Durability and Maintenance:
Consider the durability of the product, especially if you work in harsh environments. Some hearing protection devices are more robust than others.
Follow the manufacturer’s instructions for cleaning and maintenance to ensure longevity and effectiveness.
Environmental Factors:
Consider environmental factors like heat, humidity, and dust when selecting hearing protection. Some products may be better suited for specific conditions.
Training and Education:
Provide training and education to workers on the proper use of hearing protection. Ensure they know how to fit, wear, and maintain their hearing protection devices.
Regulatory Compliance:
Ensure that the selected hearing protection products comply with local regulations and standards, such as ANSI S3.19 in the United States or EN 352 in Europe.
Regular Testing:
Periodically assess the effectiveness of the chosen hearing protection through noise monitoring and hearing tests to ensure it provides adequate protection.
Consult with Experts:
If you are unsure about which hearing protection products are suitable for your specific needs, consider consulting with occupational health and safety professionals or audiologists who can provide guidance.
Remember that hearing protection is a crucial aspect of workplace safety. Choosing the right products and using them correctly can help prevent noise-induced hearing loss and protect your long-term hearing health.
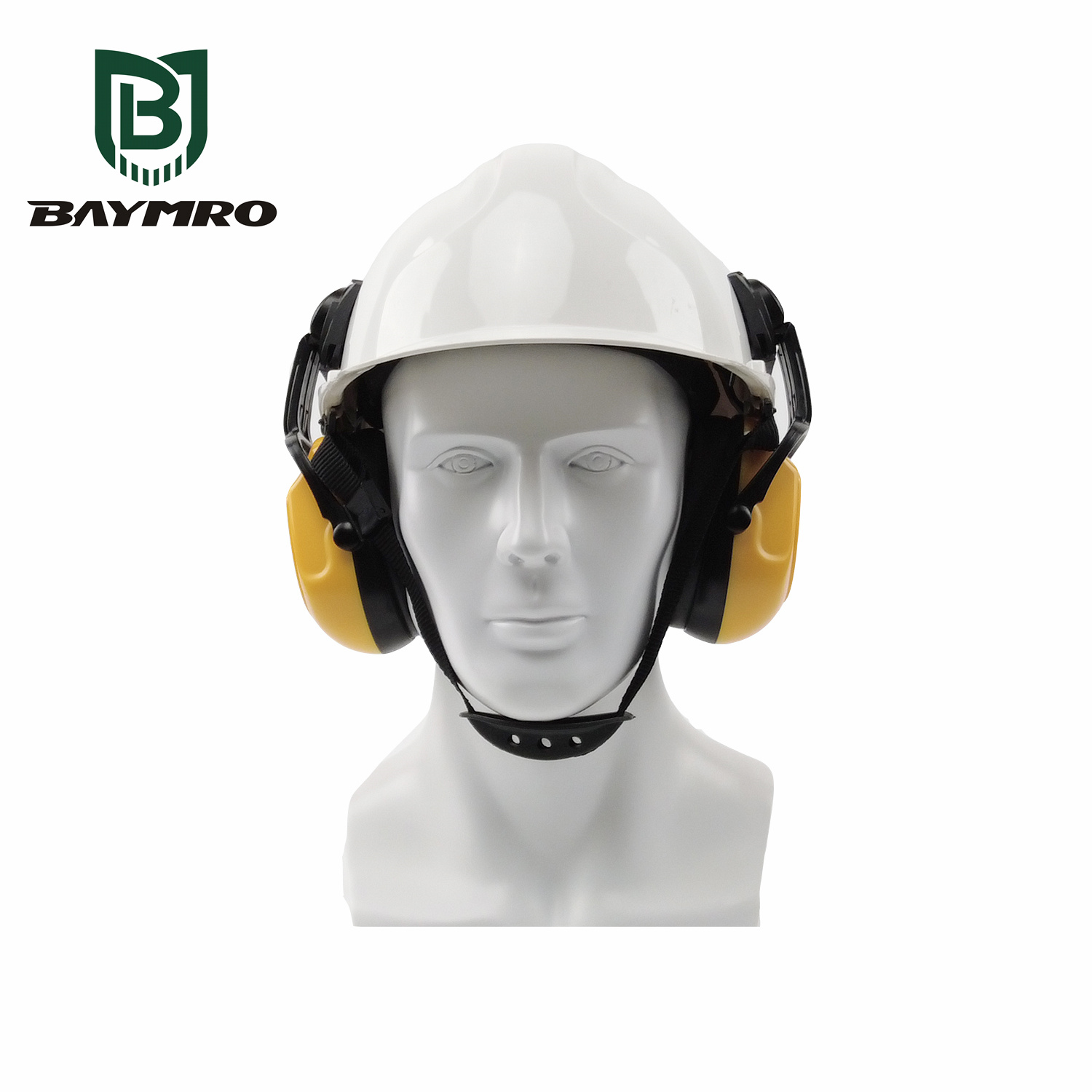
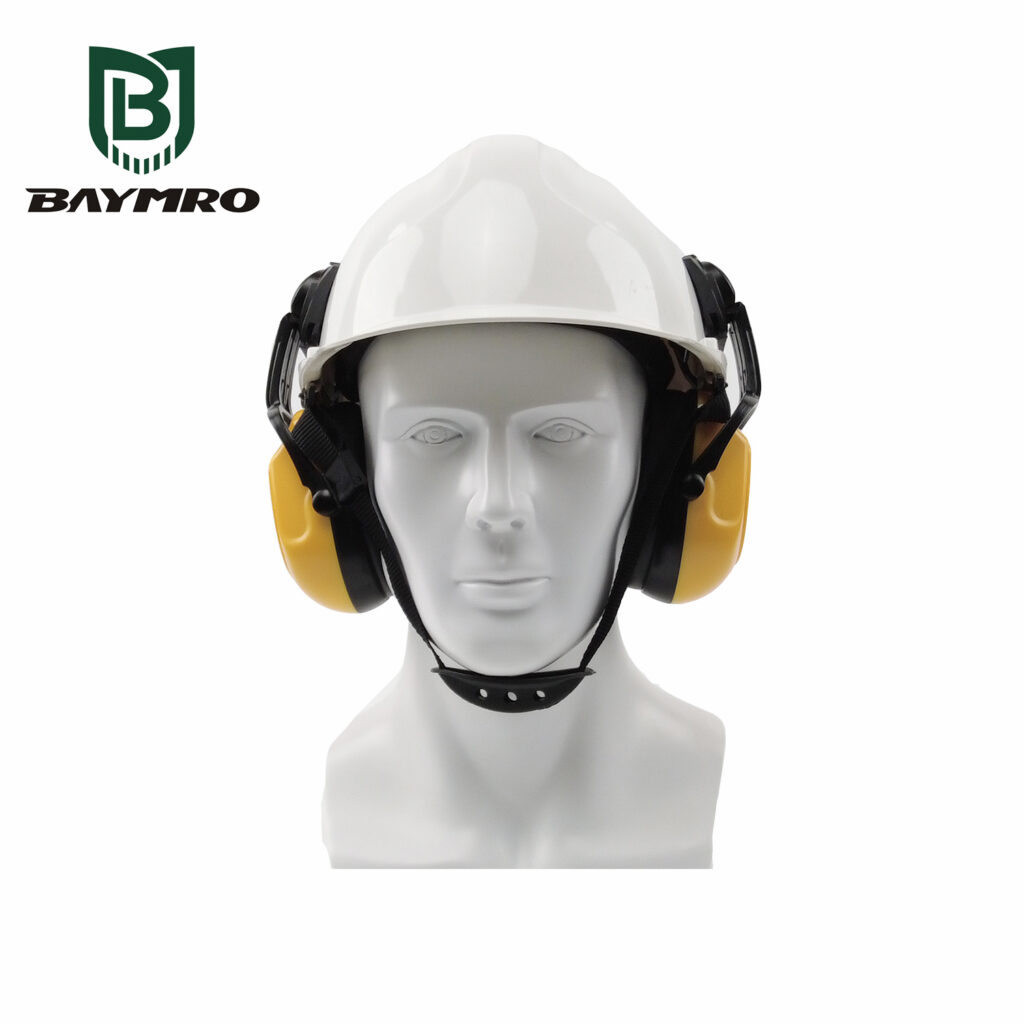
EN 352-3 is a European standard that specifically addresses ear muffs fitted to safety helmets. This standard provides requirements and testing methods for earmuffs that are integrated into industrial safety helmets, offering both hearing protection and head protection in one device. These integrated systems are commonly used in industrial and construction environments where workers are exposed to both high noise levels and potential head injury risks. Here are the key aspects of EN 352-3 for ear muffs fitted to safety helmets:
Combined Hearing and Head Protection: EN 352-3 focuses on the integration of earmuffs into industrial safety helmets, providing a comprehensive solution for workers. This combination enhances workplace safety by addressing both noise exposure and the risk of head injuries.
Noise Reduction Rating (NRR): The standard specifies minimum requirements for the noise reduction performance of the integrated earmuffs. The NRR indicates how effectively the earmuffs reduce the intensity of noise reaching the wearer’s ears. A higher NRR signifies better noise reduction capabilities.
Helmet Compatibility: EN 352-3 outlines requirements for the attachment of earmuffs to the industrial safety helmet. Ensuring compatibility with the helmet is critical to maintaining a secure and stable fit during use.
Clamping Force: The standard includes requirements for the clamping force exerted by the earmuffs on the wearer’s head. This is essential to ensure that the pressure remains within safe and comfortable limits.
Durability: EN 352-3 specifies durability requirements for the integrated system, ensuring that it can withstand the demands and conditions of the work environment.
Marking and Labeling: Earmuffs attached to safety helmets that meet EN 352-3 must be appropriately marked and labeled to indicate their compliance with the standard. This includes information such as the manufacturer’s name, model number, and noise reduction rating.
Testing Procedures: Manufacturers of ear muffs fitted to safety helmets must conduct tests as per the standard’s requirements to assess the performance of the integrated device. These tests typically include measuring noise reduction capabilities, clamping force, and durability.
EN 352-3 is particularly important in industries where both hearing protection and head protection are critical, such as construction, manufacturing, and heavy industry. By combining these two forms of protection into a single integrated system, workers can benefit from increased safety and convenience while adhering to safety and performance standards. This standard helps ensure that the integrated earmuffs and safety helmets effectively protect workers in challenging and noisy work environments.
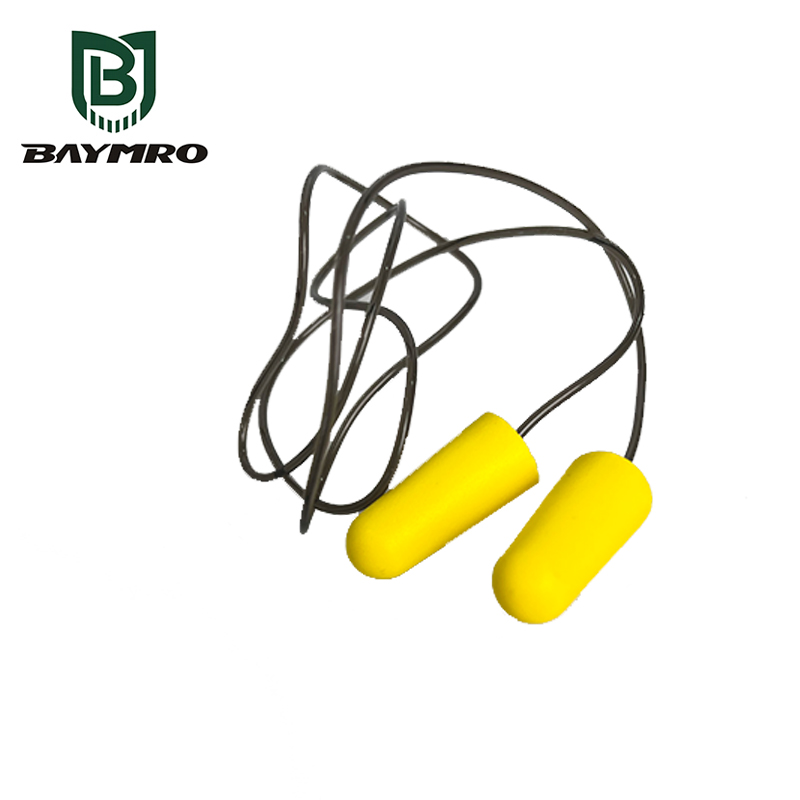
EN 352 is a series of European standards that covers various types of hearing protection devices, including earplugs. These standards specify requirements and testing methods to ensure the effectiveness and safety of hearing protection products. When it comes to earplugs, several parts of the EN 352 series are relevant:
EN 352-2: Earplugs
EN 352-2 specifically addresses earplugs used as hearing protection devices. It outlines requirements and testing methods for earplugs, including aspects such as noise reduction, comfort, durability, and safety.
EN 352-7: Level-dependent Earplugs
This part of the standard focuses on level-dependent earplugs, which are designed to offer variable protection based on noise levels. They allow wearers to hear low-level sounds, such as speech or warning signals, while protecting against high-level noise. EN 352-7 sets requirements and testing methods for such devices.
EN 352-8: Entertainment Audio Earplugs
EN 352-8 is relevant for earplugs designed for recreational or entertainment purposes, such as attending concerts or nightclubs. It addresses requirements for noise reduction and sound quality while maintaining the user’s ability to enjoy music or other forms of entertainment.
Each of these standards specifies criteria related to noise reduction, frequency range, comfort, fit, clamping force, durability, and safety. Earplug manufacturers must conform to these standards to ensure that their products provide effective hearing protection and meet safety requirements.
When selecting earplugs for hearing protection, it’s essential to consider the specific requirements of your environment and the level of noise reduction needed. Always choose earplugs that comply with the relevant EN 352 standard and follow the manufacturer’s instructions for proper fitting and use to ensure optimal protection for your hearing.

EN 352-1 does not specifically address “soundproof” earmuffs; instead, it focuses on the requirements and testing methods for hearing protection earmuffs. Earmuffs designed for hearing protection are intended to reduce the intensity of external noise reaching the wearer’s ears, but they are not typically described as “soundproof” in the sense of completely blocking out all sound.
Here’s what earmuffs designed according to EN 352-1 generally provide:
Noise Reduction: Earmuffs compliant with EN 352-1 are designed to reduce the level of external noise reaching the ears. The extent of noise reduction depends on factors such as the design of the earmuffs, the materials used, and their fit on the wearer’s head.
Comfort and Fit: EN 352-1 includes requirements for comfort and proper fit to ensure that earmuffs are comfortable for extended use and provide a good seal around the ears. Proper fit is essential for effective noise reduction.
Safety: These earmuffs are designed with safety in mind, and the standard includes requirements for clamping force to ensure that the pressure exerted on the wearer’s head is within safe limits.
Durability: Earmuffs must meet durability requirements to withstand normal wear and tear in various environments, including industrial and occupational settings.
Testing: Manufacturers of earmuffs must conduct tests according to the standard to verify the product’s performance, including its noise reduction capabilities.
While earmuffs designed to EN 352-1 specifications are effective at reducing noise levels and protecting hearing, they are not designed to create complete silence or a “soundproof” environment. The degree of noise reduction achieved depends on various factors, including the earmuff’s design, the quality of materials used, and how well they fit the wearer.
If you are looking for a product that provides a high level of soundproofing or noise isolation, you may need to consider specialized equipment such as noise-canceling headphones or custom-made hearing protection solutions. These products may not necessarily conform to EN 352-1 but are designed to block out or reduce external sounds significantly, often using active noise-canceling technology.